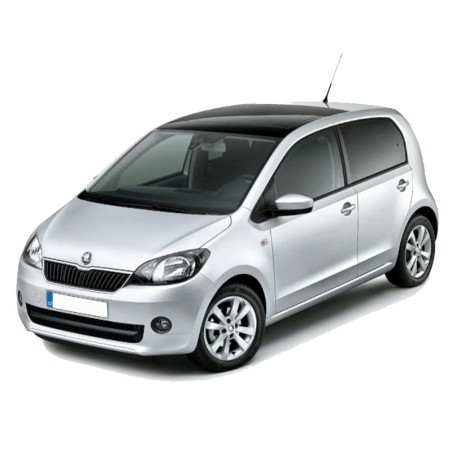
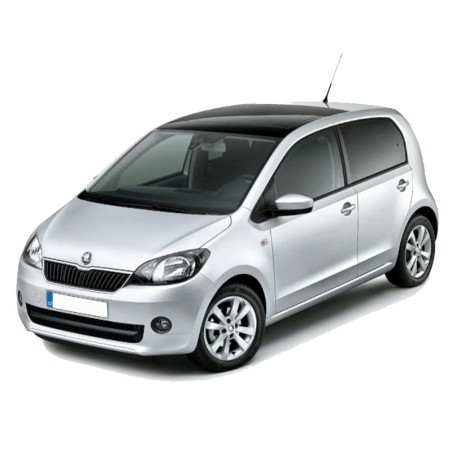
SKODA CITIGO (2011-2018) - WORKSHOP, SERVICE, REPAIR MANUAL - WIRING DIAGRAMS
- English Service Manual and Wiring Diagrams, for cars Skoda Citigo 2011 to 2018.
CONTENTS:
SERVICE MANUAL
1.0-44; 55 kW MPI engine
- 00 – Technical data
- 1 Denomination
- 1.1 Engine number
- 1.2 Engine characteristics
- 2 Safety instructions
- 2.1 Safety precautions when working on the fuel supply system
- 2.2 Safety precautions when working on vehicles with a start/stop system
- 2.3 Safety precautions during road tests in which testing and measuring equipment is used
- 2.4 Safety precautions when working on cooling system
- 2.5 Safety measures to apply when working on the fuel injection and ignition system
- 2.6 General notes on the injection system
- 2.7 General notes on the ignition system
- 2.8 Additional instructions when undertaking assembly work on the air-conditioning system
- 2.9 Safety measures and safety at work when working on vehicles with natural gas system (CNG)
- 3 Repair instructions
- 3.1 Cleanliness rules
- 3.2 Foreign bodies in the engine
- 3.3 Contact corrosion
- 3.4 Installation and fastening of lines
- 3.5 Assembly of radiators and capacitors
- 4 CNG - General
- 4.1 Valid instructions, regulations, standards and recommendations for the service, assembly and repair work on the natural gas system (CNG)
- 4.1.1 Valid instructions, regulations, standards and recommendations for the service, assembly and repair work on the natural gas system (CNG) valid for the Czech Republic
- 4.1.2 Valid instructions, regulations, standards and recommendations for the service, assembly and repair work on the natural gas system (CNG) valid for other countries
- 4.2 Inerting the natural gas fuel tank
- 4.2.1 Inerting the natural gas fuel tank with water
- 4.2.2 Inerting the natural gas fuel tank with nitrogen
- 4.3 Disposing of the natural gas fuel tank
- 4.4 Fuel tank from steel damage assessment
- 10 – Removing and installing engine
- 1 Removing and installing engine
- 1.1 Removing engine
- 1.2 Disconnect engine and gearbox
- 1.3 Securing the engine to the assembly stand
- 1.4 Installing the engine
- 2 Assembly bracket
- 2.1 Unit mounting - summary of components
- 2.2 Support the engine in its installed position
- 2.3 Removing and installing engine mount
- 2.4 Removing and installing gearbox mount
- 2.5 Removing and installing pendulum support
- 2.6 Check assembly bracket setting
- 2.7 Adjusting the unit mounting
- 13 – Crankshaft group
- 1 Cylinder block (pulley end)
- 1.1 Assembly overview - poly V-belt drive
- 1.2 Assembly overview - cylinder block (pulley end)
- 1.3 Removing and installing V-ribbed belt
- 1.3.1 Vehicles with air conditioner compressor
- 1.3.2 Vehicles without air conditioner compressor
- 1.4 Replacing crankshaft sealing ring - belt pulley end
- 2 Cylinder block on gearbox side
- 2.1 Summary of components - cylinder block on gearbox side
- 2.2 Removing and installing flywheel
- 2.3 Removing and installing sealing flange on gearbox side
- 2.3.1 Removing the sealing flange with sender wheel from the crankshaft
- 2.3.3 Attach sealing flange with rotor to the assembly tool -T10134-
- 2.3.4 Attach assembly tool -T10134- with sealing flange to the crankshaft flange and cylinder block
- 2.3.5 Secure assembly tool -T10134- to crankshaft flange
- 2.3.6 Press sender wheel onto crankshaft flange using assembly tool -T10134-
- 2.3.7 Checking sender wheel installation position on crankshaft
- 2.3.8 Re-pressing sender wheel
- 3 Crankshaft
- 4 Pistons and conrods
- 4.1 Assembly overview - piston and conrod
- 4.2 Inspect piston, piston rings and cylinder bore
- 4.3 Separating new conrod
- 15 – Cylinder head, valve gear
- 1 Cylinder head
- 1.1 Summary of components - cylinder head
- 1.2 Removing and installing camshaft housing
- 1.2.1 Removing and installing camshaft housing until 05.2012
- 1.2.2 Removing and installing camshaft housing as of 06.2012
- 1.3 Removing and installing the cylinder head
- 1.4 Testing the compression
- 2 Toothed belt drive
- 2.1 Position crankshaft to “TDC” .
- 2.2 Checking valve timing
- 2.3 Remove the toothed belt from the camshafts
- 2.3.1 Remove the toothed belt from the camshafts up to 05.2012
- 2.3.2 Remove the toothed belt from the camshafts from 06.2012
- 2.4 Removing and installing toothed belt
- 2.4.1 Removing and installing toothed belt up to 05.2012
- 2.4.2 Removing and installing toothed belt as of 06.2012
- 3 Valve gear
- 3.1 Assembly overview - valve gear
- 3.2 Measuring the axial play of the camshafts
- 3.3 Removing and installing camshaft control
- 3.4 Removing and installing camshaft sprocket
- 3.5 Removing and installing gasket ring for camshaft
- 3.5.1 Removing and installing the sealing ring for camshafts on the belt pulley side
- 3.5.2 Removing and installing the gasket ring for camshaft on the belt pulley side
- 3.6 Replacing valve stem seals
- 4 Inlet and exhaust valves
- 4.1 Inspect valve guides
- 17 – Lubrication
- 1 Lubrication system
- 1.1 Summary of components - lubrication system
- 1.2 Removing and installing oil pan
- 1.3 Removing and installing oil pump
- 2 Crankcase ventilation
- 2.1 Summary of components - crankcase ventilation
- 2.2 Removing and installing oil separator
- 3 Oil filter, oil pressure switch
- 3.1 Removing and installing oil filter housing
- 3.2 Removing and installing oil pressure switch -F1-
- 3.3 Testing oil pressure and oil pressure switch -F1-
- 19 – Cooling
- 1 Cooling system
- 1.1 Connection diagram for coolant hoses
- 1.2 Checking the coolant system for leak tightness
- 1.3 Draining and filling up coolant
- 1.3.1 Draining coolant
- 1.3.2 Filling with coolant
- 2 Coolant pump, regulation of cooling system
- 2.1 Assembly overview - coolant pump
- 2.2 Assembly overview - thermostat
- 2.3 Removing and installing coolant pump
- 2.4 Removing and installing coolant regulator
- 2.4.1 Removing and installing thermostat (extended circuit)
- 2.4.2 Removing and installing thermostat (small circuit)
- 2.5 Removing and installing toothed belt for coolant pump
- 2.6 Removing and installing coolant temperature sender
- 2.6.1 Removing and installing coolant temperature sender -G62-
- 2.6.2 Removing and installing radiator fan thermal switch -F18-
- 3 Radiator and radiator fan
- 3.1 Summary of components - Parts of the cooling system fitted to body
- 3.2 Removing and installing radiator
- 3.3 Removing and installing radiator cowling with radiator fan
- 3.4 Removing and installing radiator fan
- 20 – Fuel supply system
- 1 Fuel system
- 1.1 Overview of fitting locations - fuel supply
- 2 Fuel tank/natural gas container
- 2.1 Summary of components - fuel tank for petrol only vehicles
- 2.2 Summary of components - fuel tank for natural gas vehicles (CNG)
- 2.3 Summary of components - Natural gas container
- 2.3.1 Summary of components - Natural gas container 1
- 2.3.2 Summary of components - Natural gas container 2
- 2.3.3 Summary of components - tensioning strap and spring package
- 3 Petrol fuel system
- 3.1 Summary of components - fuel system pressurisation pump -G6-.
- 3.2 Removing and installing fuel delivery unit only for petrol vehicles
- 3.3 Removing and installing the fuel delivery unit for natural gas vehicles (CNG)
- 3.4 Removing and installing the sender for fuel gauge display -G-
- 3.5 Removing and installing fuel tanks only for petrol vehicles
- 3.6 Removing and installing the fuel tank for natural gas vehicles (CNG)
- 3.7 Fuel filter
- 3.8 Testing fuel pump
- 3.8.1 Checking fuel pressure
- 3.8.2 Testing holding pressure
- 3.8.3 Check fuel flow rate
- 3.9 Drain the fuel tank
- 3.9.1 Emptying fuel tank when fuel pump is intact
- 3.9.2 If the fuel pump has a fault, and the fuel tank is filled by more than 3/4 if there is a fault to the fuel pump.
- 3.9.3 If the fuel pump has a fault, and the fuel tank is filled by less than 3/4 if there is a fault to the fuel pump.
- 4 Quick couplings
- 4.1 Separating quick couplings
- 5 Natural gas fuel system (CNG)
- 5.1 Summary of components - seal fuel tank
- 5.2 Summary of components - filling connection
- 5.3 Mechanically close the tank shut-off valves -N361/N362-
- 5.4 Remove the pressure in the high-pressure line
- 5.5 Removing and installing natural gas container
- 5.5.1 Removing and installing natural gas container 1
- 5.5.2 Removing and installing natural gas container 2
- 5.6 Removing and installing solenoid coil of tank shut-off valve-N361/N362-
- 5.7 Empty the natural gas container
- 5.8 Determine the residual pressure in the natural gas container
- 5.8.1 Check and rework the adapter for the residual pressure test of the natural gas
- 5.8.2 Test (self-test) the cooling system tester -V.A.G 1274 B- and the adapter for the cooling system tester -V.A.G 1274 B/12 A-
- 5.8.3 Residual pressure test of the natural gas
- 5.9 Removing and installing tank shut-off valve -N361/N362-
- 5.10 Removing and installing filling connection
- 6 Accelerator pedal
- 6.1 Assembly overview - accelerator module
- 6.2 Removing and installing accelerator pedal module -GX2-
- 7 Activated charcoal container system
- 7.1 Assembly overview - activated charcoal filter system
- 7.1.1 Summary of components - Activated charcoal filter only for petrol vehicles
- 7.1.2 Summary of components - Activated charcoal filter system for natural gas vehicles (CNG)
- 7.2 Checking the fuel tank venting
- 7.3 Removing and installing activated charcoal filter
- 24 – Mixture preparation - injection
- 1 Fuel Injection System
- 1.1 Summary of components - injection system
- 1.1.1 Summary of components - engine from front
- 1.1.2 Summary of components - engine from rear
- 1.2 Assembly overview - fuel system
- 2 Injectors
- 2.1 Assembly overview - fuel rail with injectors
- 2.2 Removing and installing injection valves
- 2.3 Testing injection valves
- 3 Checking leak-tightness of the natural gas fuel supply system
- 3.1 Differentiating pressure area of the natural gas fuel supply system
- 3.1.1 High-pressure system
- 3.1.2 Low-pressure area
- 3.2 Determine the pressure in the natural gas system
- 3.3 Determining the operating mode of natural gas vehicles
- 3.4 Deactivating/activating natural gas mode
- 3.5 Inspecting the liquefied petroleum gas system (LPG) for leak tightness
- 3.5.1 Checking gas system for leak-tightness, after work on the high-pressure system
- 3.5.2 Checking gas system for leak-tightness, after work in the low-pressure area
- 4 Gas pressure regulator
- 4.1 Summary of components - gas pressure regulator
- 4.2 Removing and installing gas pressure regulator
- 4.3 Removing and installing the tank pressure sensor -G400-
- 5 Gas inlet valves
- 5.1 Summary of components - gas distribution line with gas inlet valves
- 5.2 Removing and installing gas distribution line with gas inlet valves -N366-, -N367-, -N368-
- 5.3 Removing and installing the gas distribution line sensor -G401-
- 6 Air filter
- 6.1 Assembly overview - air filter housing
- 6.2 Removing and installing air filter housing
- 7 Intake manifold
- 7.1 Assembly overview - intake manifold
- 7.2 Removing and installing intake manifold
- 7.3 Removing and installing the throttle valve control unit -GX3-
- 7.4 Clean throttle valve control unit -GX3-
- 8 Senders and sensors
- 8.1 Removing and installing intake manifold pressure sender -G71- with intake air temperature sender -G42-
- 9 Engine control unit
- 9.1 Assembly overview - engine control unit
- 9.2 Removing and installing engine control unit
- 9.2.1 Removing and installing engine control unit -J623-
- 9.2.2 Removing and installing theft-protected engine control unit -J623-
- 9.2.3 Removing engine control unit from bracket
- 10 Lambda probe
- 10.1 Removing and installing lambda probe - catalytic converter on engine
- 10.1.1 Removing and installing Lambda probe 1 after catalytic converter -GX7-
- 10.1.2 Removing and installing Lambda probe 1 after catalytic converter -GX10-
- 10.2 Removing and installing lambda probe - catalytic converter on bottom of vehicle
- 26 – Exhaust system
- 1 Removing and installing parts of the exhaust system
- 1.1 Summary of components - Pre-exhaust pipe with catalytic converter
- 1.1.1 Summary of components - pre-exhaust pipe with catalytic converter on engine
- 1.1.2 Summary of components - pre-exhaust pipe with catalytic converter on bottom of vehicle
- 1.2 Summary of components - Middle and rear part of the exhaust system
- 1.2.1 Replace middle or rear part of the exhaust system on petrol vehicles only
- 1.2.2 Summary of components - Replace middle or rear part of the exhaust system on natural gas vehicles CNG
- 1.3 Removing and installing pre-exhaust pipe with catalytic converter
- 1.3.1 Order of installation for pre-exhaust pipe with catalytic converter on engine
- 1.4 Separating the exhaust pipe
- 1.5 Removing and installing middle and rear silencers
- 1.6 Installation position of clamping sleeve
- 28 – Ignition system
- 1 Ignition system
- 1.1 Assembly overview - ignition system
- 1.2 Removing and installing ignition coils with power output stages
- 1.3 Removing and installing knock sensor 1 -G61-
- 1.4 Removing and installing Hall sender
- 1.5 Removing and installing engine speed sender
Air Conditioning System With Refrigerant R123yf
- 00 – Technical data
- 1 Safety instructions
- 1.1 Safety precautions when working on air Conditioning systems
- 1.2 Safety precautions when handling refrigerants
- 1.3 Safety precautions when working on vehicles with a start/stop system
- 1.4 Safety precautions when handling AC service stations
- 1.5 Safety precautions when handling pressurised containers
- 2 Laws and regulations
- 2.1 Regulations and directives
- 2.2 Filling a refrigerant circuit with other refrigerants
- 2.3 Safety at work
- 3 Repair notes
- 3.1 Cleanliness rules
- 3.2 Seals for the refrigerant circuit
- 3.3 Refrigerant and refrigerant oil
- 3.3.1 Important instructions for repairs involving refrigerant and refrigerant oil
- 3.3.2 Refrigerant machine oil
- 3.4 Handling pressurised containers
- 3.5 Handling refrigerant
- 4 Identification
- 4.1 Information plate for refrigerant circuit
- 5 Technical data
- 5.1 Filling capacities for refrigerant
- 5.2 Filling capacities for refrigerant oil
- 6 Technical and physical principles
- 6.1 Principles of the air-conditioning technology
- 6.1.1 Physical principles of the air conditioning system
- 6.1.2 Pressure and boiling point of the refrigerant
- 6.1.3 Vapour pressure table for the refrigerant
- 6.2 Physical properties
- 6.2.1 Refrigerant R1234yf
- 6.2.2 Potential hazards of refrigerant R1234yf
- 6.2.3 Physical and chemical properties of refrigerant R1234yf
- 6.2.4 Critical point
- 6.2.5 Environmental aspects of refrigerant R1234yf
- 6.2.6 Trade names and designations of refrigerant R1234yf
- 6.2.7 Colour and odour of refrigerant R1234yf
- 6.2.8 Vapour pressure of refrigerant R1234yf
- 6.2.9 Physical properties of refrigerant R1234yf
- 6.2.10 Behaviour of refrigerant R1234yf in contact with metals and plastics
- 6.2.11 Critical temperature/critical pressure of refrigerant R1234yf
- 6.2.12 Water content of refrigerant R1234yf
- 6.2.13 Flammability/decomposition of refrigerant R1234yf
- 6.2.14 Filling factor of refrigerant R1234yf
- 6.2.15 Evidence of leaks in a refrigerant circuit with refrigerant R1234yf
- 6.2.16 Analysis of refrigerant R1234yf
- 6.3 Product features
- 6.4 Function and purpose of the air conditioning system
- 6.4.1 Operating principle
- 6.4.2 Comfort
- 6.4.3 Environmental aspects
- 6.5 Further sources of information
- 87 – Air conditioning system
- 1 Refrigerant circuit
- 1.1 System overview - refrigerant circuit
- 1.2 General description – components of the refrigerant circuit
- 1.2.1 Arrangement and function of the refrigerant circuit
- 1.2.2 AC compressor
- 1.2.3 Condenser
- 1.2.4 Evaporator
- 1.2.5 Fluid reservoir
- 1.2.6 Expansion valve
- 1.2.7 Refrigerant pipe with internal heat exchanger
- 1.2.8 Gaskets
- 1.2.9 Pipes and hoses of the refrigerant circuit
- 1.2.10 Pressure relief valve
- 1.2.11 Connections for quick couplers on refrigerant circuit
- 1.2.12 Connections with valve for switches on refrigerant circuit
- 1.2.15 Regulating valve for compressor of air conditioning system -N280-
- 1.3 Possible complaints
- 1.3.1 Requirements for investigating a complaint
- 1.3.2 Possible complaints
- 1.3.3 Odour from the heating and air conditioning unit
- 1.4 Identifying leaks
- 1.4.1 General information about finding leaks in the refrigerant circuit
- 1.4.2 Detecting leaks on refrigerant circuits with an electronic leak detector
- 1.4.3 Searching for leaks with the UV leak detection system
- 1.4.4 Detecting leaks by means of vacuum testing with the AC service station or pressure testing
- 1.5 Replace components
- 1.5.1 General instructions for replacing components
- 1.5.2 Replacing leaking or damaged components; empty refrigerant circuit (except AC compressor and fluid reservoir)
- 1.5.3 Replacing leaking or damaged components; filled refrigerant circuit (except AC compressor and fluid reservoir)
- 1.5.4 Replacing the AC compressor without needing to clean the refrigerant circuit
- 1.5.5 Replacing the AC compressor because of a leak or internal damage
- 1.6 Clean the refrigerant circuit.
- 1.6.1 General information about cleaning the refrigerant circuit
- 1.6.2 Preparing to clean the refrigerant circuit (to flush with refrigerant R1234yf)
- 1.6.3 Procedure for cleaning the refrigerant circuit
- 1.6.4 Schematic diagrams for cleaning (circuits to be flushed) - refrigerant circuit with expansion valve and fluid reservoir
- 1.6.5 Adapter for setting up the rinsing cycles
- 1.6.6 General information about blowing through with compressed air or nitrogen
- 1.6.7 Blowing through the refrigerant circuit with compressed air and nitrogen
- 1.7 Checking pressures with the pressure gauge
- 1.7.2 Pressure gauges allow to carry out the following inspection and measurement work
- 2 Working with the A/C service station
- 2.1 Working with the A/C service station
- 2.2 Connecting the AC service station to the refrigerant circuit
- 2.3 Performing gas analysis for the refrigerant
- 2.4 Exhaust refrigerant circuit.
- 2.5 Evacuating the refrigerant circuit.
- 2.6 Filling the refrigerant circuit
- 2.7 Operate the air conditioning system after filling
- 2.8 Switching off the AC service station and disconnecting it from the refrigerant circuit
- 2.9 Filling refrigerant into the reservoir
- 2.10 Draining the A/C service station
- 2.11 Clean the refrigerant circuit.
- 2.12 Filling contaminated refrigerant into a recycling cylinder for analysis, treatment or disposal
- 2.13 Check pressures
- 2.13.1 General instructions for checking pressures in a refrigerant circuit
- 2.13.2 Pressures and temperatures in a refrigerant circuit
- 2.13.3 Pressure in a refrigerant circuit when the ignition is switched off
- 2.13.4 Checking pressures when the air conditioning system is switched on
- 3 Test equipment and tools
- 3.1 Tools and materials available from the importer
- 3.2 Tools and materials, which are commercially available
- 3.3 Tools that can be made instead of purchasing
Air Conditioning System With Refrigerant R134a
- 00 – Technical data
- 1 General notes on the air conditioning system
- 1.1 Important instructions
- 1.2 Further documentation and information means
- 1.3 Principles of the air-conditioning technology
- 1.3.1 Physical principles
- 1.3.2 Heat always flows from a warmer substance to a colder substance
- 1.3.3 Pressure and boiling point
- 1.4 Advantages of the air conditioning system - comfort
- 1.5 Operation of the air conditioning system
- 1.6 Refrigerant R134a
- 1.6.1 Physical data of the refrigerant R134a
- 1.6.2 Trade names and designations of the refrigerant R134a
- 1.6.3 Critical point
- 1.6.4 Environmental aspects of the refrigerant R134a
- 1.7 Vapour pressure table for refrigerant R134a
- 1.8 Properties of refrigerant R134a
- 1.8.1 Colour
- 1.8.2 Vapour pressure
- 1.8.3 Air displacement as a result of gaseous refrigerant
- 1.8.4 Behaviour with metals
- 1.8.5 Behaviour with plastics
- 1.8.6 Critical temperature/critical pressure
- 1.8.7 Water content
- 1.8.8 Flammability
- 1.8.9 Filling factor
- 1.9 Evidence of leaks
- 1.10 Refrigerant oil
- 1.10.1 Properties of the refrigerant oil
- 1.11 General occupational safety
- 1.11.1 Product features
- 1.11.2 Using refrigerant R 134a
- 1.11.3 Wear safety goggles
- 1.11.4 Wear protective gloves and apron
- 1.11.5 Do not breath in refrigerant vapours
- 1.11.6 Smoking ban
- 1.11.7 Welding and soldering
- 1.11.8 Pungent odour
- 1.11.9 First Aid
- 1.12 Using pressure tank
- 1.13 Safety precautions when working with extraction and filling systems
- 1.14 Safety measures when working on vehicles with air conditioning system and when using refrigerant R 134a
- 1.15 Basics for working on the refrigerant circuit
- 1.15.1 General points
- 1.15.2 Removing contaminants from the refrigerant circuit
- 1.15.3 Additional work on vehicles with AC compressor without magnetic coupling
- 1.15.5 Work procedure before operating the air conditioning system after a repair
- 2 General instructions for refrigerant circuit
- 2.1 Components of the refrigerant circuit
- 2.1.1 Distribution of the components of the refrigerant circuit and their influence on the high- and low-pressure side
- 2.1.2 AC compressor
- 2.1.4 Fluid reservoir with desiccator
- 2.1.8 O-ring seals
- 2.1.9 Pipes and hoses of the refrigerant circuit
AND MORE.....