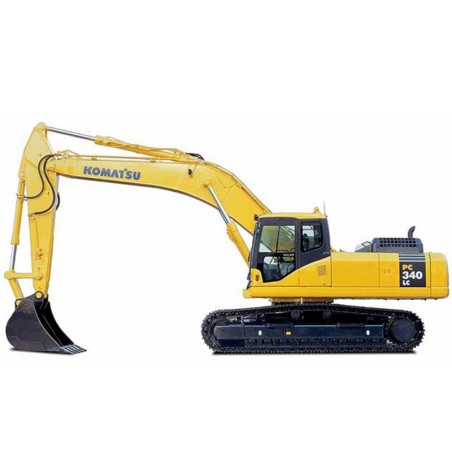
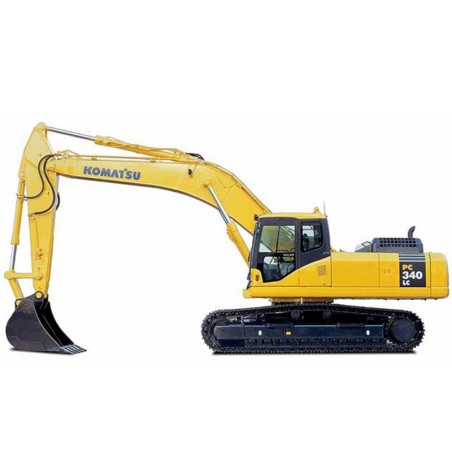
KOMATSU PC340LC, 340NLC-7K - WORKSHOP, SERVICE, REPAIR MANUAL - WIRING DIAGRAMS
- English Service Manual and Wiring Diagrams, to Komatsu PC340LC, 340NLC-7K.
CONTENTS:
PC340LC-7
PC340NLC-7
40001 AND UP
40001 AND UP
PC340 07 SECTION01
- specification dimension drawings
- dimensions
- working ranges
- dimensions
- working ranges
- specifications
- pc340lc-7, pc340nlc-7
- weight table
- pc340lc-7, pc340nlc-7
- fuel, coolant, and lubricants
PC340 7 SECTION10
- engine related parts
- radiator • oil cooler • aftercooler
- power train
- final drive
- swing machinery
- swing circle
- track frame • recoil spring
- idler
- carrier roller
- track roller
- track shoe
- triple grouser shoe
- hydraulic equipment layout drawing
- hydraulic tank
- hydraulic pump
- hpv125 + 125
- ls valve
- pc valve
- ls(pc)-epc valve
- variable volume valve
- control valve
- main relief valve
- variable pressure compensation valve
- clss
- outline of clss
- self pressure reducing valve
- swing motor
- reverse prevention valve
- center swivel joint
- travel motor
- travel junction valve
- travel ppc shuttle valve
- valve control
- work equipment • swing ppc valve
- travel ppc valve
- service ppc valve
- solenoid valve
- ppc accumulator
- return oil filter
- for breaker
- boom hydraulic drift prevention valve
- quick return valve
- lift check valve
- attachment circuit selector valve
- hydraulic cylinder
- boom cylinder
- arm cylinder
- bucket cylinder
- work equipment
- 2. dimension of bucket
- air conditioner
- air conditioner piping
- engine control
- governor motor
- engine throttle and pump controller
- electronic control system
- total system diagram
- multi monitor system
- sensor
20-001
- 1. the standard value for a new machine given in the table is the value used when shipping the ma...
- 2. the service limit value given in the tables is the estimated value for the shipped machine bas...
- 3. these standard values are not the standards used in dealing with claims.
- standard value table for engine related parts
- standard value table for chassis related parts
20 101
- inspection and adjustment of engine rpm
- measurement of air boost pressure
- measurement of exhaust gas color
- adjustment of valve clearance
- measurement of compression pressure
- measurement of blow-by pressure
- inspection and adjustment of fuel injection timing
- measurement of engine oil pressure
- adjustment of engine speed sensor
- inspection and adjustment of air compressor belt tension
- emergent escape from failure in engine control system
- measurement of clearance in swing circle bearings
- inspection and adjustment of track shoe tension
- inspection of wear on sprocket
- inspection and adjustment of hydraulic oil pressure in hydraulic circuit for work equipment, swin...
- inspection and adjustment of control circuit oil pressure
- inspection and adjustment of pump pc control circuit oil pressure
- inspection and adjustment of pump ls control circuit oil pressure
- measurement of solenoid valve output pressure
- measurement of ppc valve output pressure
- adjustment of work equipment and swing ppc valve
- inspection of locations of hydraulic drift of work equipment
- release of remaining pressure in hydraulic circuit
- measurement of oil leakage amount
- air bleeding of various parts
- inspection procedures for diode
- special function of multi-monitor panel
- display method and special functions of 7-segment monitor panel
- preparations for troubleshooting electrical system
20 201
- points to remember when troubleshooting
- sequence of events in troubleshooting
- points to remember when carrying out maintenance
- checks before troubleshooting
- classification and steps for troubleshooting
- connector location chart and electrical circuit diagram by system
- connection table for connector pin numbers
20 301
- information contained in troubleshooting table
20 501
- information contained in troubleshooting table
30
- how to read this manual
- removal and installation of assemblies
- disassembly and assembly of assemblies
- precautions when performing operation
- removal and installation of starting motor assembly
- removal
- installation
- removal and installation of fuel injection pump assembly
- removal and installation of engine front seal
- removal and installation of engine rear seal
- removal and installation of cylinder head assembly
- removal and installation of radiator assembly
- removal and installation of hydraulic oil cooler assembly
- removal and installation of engine and hydraulic pump assemblies
- removal and installation of final drive assembly
- disassembly and assembly of final drive assembly
- sketches of special tools
- removal and installation of swing motor, swing machinery assembly
- disassembly and assembly of swing motor, swing machinery assembly
- sketches of special tools
- disassembly and assembly of carrier roller assembly
- disassembly and assembly of track roller assembly
- disassembly and assembly of idler assembly
- disassembly and assembly of recoil spring assembly
- removal and installation of track shoe assembly
- expansion of track shoe
- removal and installation of swing circle assembly
- removal and installation of revolving frame assembly
- removal and installation of center swivel joint assembly
- disassembly and assembly of center swivel joint assembly
- removal and installation of hydraulic tank assembly
- removal and installation of control valve assembly
- disassembly and assembly of control valve assembly
- removal and installation of hydraulic pump assembly
- removal and installation of oil seal in hydraulic pump input shaft
- disassembly and assembly of work equipment ppc valve assembly
- disassembly and assembly of travel ppc valve assembly
- disassembly and assembly of hydraulic cylinder assembly
- removal and installation of work equipment assembly
- removal and installation of air conditioner unit assembly
- removal and installation of counterweight assembly
- removal and installation of operator’s cab assembly
- removal and installation of monitor assembly
- removal and installation of governor pump controller assembly
20 601
- troubleshooting of hydraulic and mechanical system (h-mode)
- system chart for hydraulic and mechanical systems
- information contained in troubleshooting table
- h-1 all work equipment lack power, or travel and swing speeds are slow
- h-2 engine speed sharply drops or engine stalls
- h-3 no work equipment, travel or swing move
- h-4 abnormal noise is heard from around hydraulic pump
- h-5 auto-decelerator does not work
- h-6 fine control mode does not function
- h-7 boom moves slowly or lacks power
- h-8 arm moves slowly or lacks power
- h-9 bucket moves slowly or lacks power
- h-10 work equipment does not move in its single operation
- h-11 work equipment has a bit too fast hydraulic drift
- h-12 work equipment has big time lag
- h-13 other work equipment moves when relieving single circuit
- h-14 one-touch power max. switch does not operate
- h-15 in compound operation, work equipment with larger load moves slowly
- h-16 in swing + boom raise operation, boom moves slowly
- h-17 in swing + travel, travel speed drops sharply
- h-18 machine swerves in travel
- h-19 machine travels slowly
- h-20 machine cannot be easily steered or lacks power
- h-21 travel speed does not shift, or it is too slow or fast.
- h-22 track shoe does not turn (on one side only)
- h-23 machine does not swing
- h-24 swing acceleration is poor, or swing speed is slow
- h-25 excessive overrun when stopping swing
- h-26 there is big shock when stopping swing
- h-27 there is big abnormal noise caused when stopping swing
- h-28 swing natural drift is too big
PC340 A2
- hydraulic circuit diagram
- electrical circuit diagram (1/4)
- for multi monitor
- electrical circuit diagram (2/4)
- for multi monitor
- electrical circuit diagram (3/4)
- for multi monitor
- electrical circuit diagram (4/4)
- for multi monitor