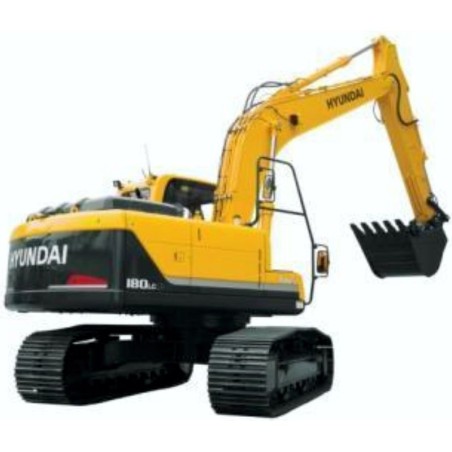
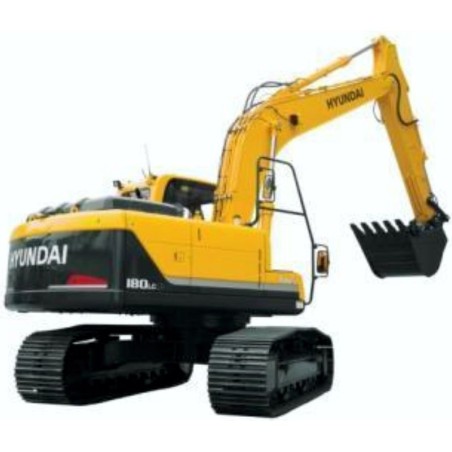
HYUNDAI R180LC-7 - WORKSHOP, SERVICE, REPAIR MANUAL - OPERATORS MANUAL - WIRING DIAGRAMS
- English Service Manual, Operators Manual and Wiring Diagrams, for Crawler Excavator Hyundai R180LC-7.
CONTENTS:
SERVICE MANUAL
- FOREWORD
- CONTENTS
- SECTION 1
- GENERAL
- Group 1 Safety Hints
- Group 2 Specifications
- SECTION 2
- STRUCTURE
- Group 1 Pump Device
- Group 2 Main Control Valve
- Group 3 Swing Device
- Group 4 Travel Device
- Group 5 RCV Lever
- Group 6 RCV Pedal
- SECTION 3
- HYDRAULIC SYSTEM
- Group 1 Hydraulic Circuit
- Group 2 Main Circuit
- Group 3 Pilot Circuit
- Group 4 Single Operation
- Group 5 Combined Operation
- SECTION 4
- ELECTRICAL SYSTEM
- Group 1 Component Location
- Group 2 Electrical Circuit
- Group 3 Electrical Component Specification
- Group 4 Connectors
- SECTION 5
- MECHATROMICS SYSTEM
- Group 1 Outline
- Group 2 Mode selection System
- Group 3 Travel Speed Control System
- Group 4 Automatic Warming Up Function
- Group 5 Engine Overheat Prevention Function
- Group 6 Automatic Warming Up Function
- Group 7 Self-Diagnostic System
- Group 8 Engine Control System
- Group 9 Monitoring System
- SECTION 6
- TROUBLESHOOTING
- Group 1 Before troubleshooting
- Group 2 Hydraulic and Mechanical System
- Group 3 Electrical System
- Group 4 Mechatronics System
- SECTION 7
- MAINTENANCE STANDARD
- Group 1 Operational Performance Test
- Group 2 Major Components
- Group 3 Track and Work Equipment
- SECTION 8
- DISASSEMBLY AND ASSEMBLY
- Group 1 Precaution
- Group 2 Tightening Torque
- Group 3 Pump Device
- Group 4 Main Control Valve
- Group 5 Swing Device
- Group 6 Travel Device
- Group 7 RCV Lever
- Group 8 Turning Joint
- Group 9 Boom, Arm and Bucket Cylinder
- Group 10 Undercarriage
- Group 11 Work Equipment
- SECTION 9
- COMPONENT MOUNTING TORQUE
- Group 1 Introduction guide
- Group 2 Engine system
- Group 3 Electric system
- Group 4 Hydraulic system
- Group 5 Undercarriage
- Group 6 Structure
- Group 7 Work equipment
ENGINE SERVICE MANUAL
- BINDING
- INTRODUCTION
- How to use this manual
- Methods of presentation
- Terms used in this manual
- Abbreviations
- Units of measurement
- Safety Cautions
- Fire and explosion
- Keep flames away
- Keep surrounding area tidy and clean
- Avoid accessing crankcase until engine cools
- Care about fuel, oil and exhaust gas leakage
- Use explosion-proof lighting apparatus
- Prevent electrical wires from short-circuiting
- Keep fire extinguishers and first-aid kit handy
- Stay clear of all rotating and moving parts
- Install protective covers on rotating parts
- Ensure safety of neighboring people before starting engine
- Stay clear of moving parts during engine running
- Lockout and tagout
- Keep engine stopped during servicing
- Always restore engine turning tools after use
- Be careful of burns
- Do not touch the engine during or immediately after operation
- Slowly and carefully open radiator cap
- Add coolant only after the coolant temperature dropped
- Never remove heat shields
- Be careful of exhaust fume poisoning
- Operate engine in well-ventilated area
- Protect ears from noises
- Wear ear plugs
- Be careful of falling down
- Lift engine correctly
- Do not climb onto the engine
- Establish firm scaffold during work
- Be careful of handling fuel, engine oil and LLC
- Use only specified fuel, engine oil and long- life coolant (LLC)
- Handle LLC (long life coolant) carefully
- Proper disposal of waste oil and coolant (LLC)
- Service battery
- Handle the battery correctly
- When abnormality occurs
- Stop overheated engine after cooling run
- Avoid immediate restart after abnormal stop
- Avoid continuous engine operation with too low oil pressure
- Stop the engine immediately if the fan belt breaks
- Other cautions
- Modification of engine prohibited
- Never break the seals
- Pre-operational check and periodic inspection/maintenance
- Break-in operation
- Warming-up operation
- Avoid engine operations in a overload condition
- Cooling operation before stopping engine
- Protection of engine against water entry
- Maintenance of air cleaner or pre-cleaner
- Observe safety rules at work site
- Work clothing and protective gear
- Use of tools optimum for each work
- Avoidance of prolonged time of starter operation
- Do not turn off battery switch during operation
- Cautionary instructions for transporting engine
- Avoid continuous engine operation in a low load condition
- Ventilation of engine room
- Avoid contact with high-pressured fuel
- About warning labels
- Maintenance of warning labels
- GENERAL CONTENTS
- GENERAL
- 1. External view
- 2. System flow diagrams
- 2.1 Fuel system - flow diagram
- 2.2 Lubrication system - flow diagram
- 2.3 Cooling system - flow diagram
- 2.4 Inlet and exhaust system - flow diagram
- 3. Engine serial number location
- 4. Main specifications
- 5. Tips on disassembling and reassembling
- 5.1 Disassembling
- 5.2 Reassembling
- SERVICE DATA
- 1. Maintenance service data
- 1.1 General
- 1.2 Basic engine
- 1.3 Fuel system
- 1.4 Lubrication system
- 1.5 Cooling system
- 1.6 Inlet and exhaust system
- 1.7 Electrical system
- 2. Tightening torque table
- 2.1 Major bolt tightening torque
- 2.1.1 Basic engine
- 2.1.2 Fuel system
- 2.1.3 Lubrication system
- 2.1.4 Cooling system
- 2.1.5 Inlet and exhaust systems
- 2.1.6 Electrical system
- 2.2 Standard bolt and nut tightening torque
- 2.2.1 Metric automobile screw thread
- 2.2.2 Metric course screw thread
- 2.3 Standard stud tightening torque
- 3. Regarding submission of parts for EPA exhaust gas regulation
- SERVICE TOOLS
- 1. Special tool
- DETERMINATION OF OVERHAUL
- 1. Determining overhaul timing
- 2. Testing compression pressure
- DISASSEMBLY OF BASIC ENGINE
- 1. Disassembling and inspecting cylinder head and valve mechanism
- 1.1 Removing rocker shaft assembly
- 1.2 Disassembling rocker shaft assembly
- 1.3 Removing cylinder head bolt
- 1.4 Removing cylinder head assembly
- 1.5 Removing valve and valve spring
- 1.6 Removing valve stem seal
- 2. Disassembling and inspecting flywheel
- 2.1 Removing flywheel
- 2.2 Removing rear plate
- 3. Disassembling and inspecting damper, gear case, timing gear and camshaft
- 3.1 Removing crankshaft pulley and damper
- 3.2 Removing cover
- 3.3 Removing timing gear case
- 3.4 Measuring timing gear backlash
- 3.5 Measuring idler gear and camshaft gear end play
- 3.6 Removing fuel injection pump
- 3.7 Removing oil pan
- 3.8 Removing oil strainer
- 3.9 Removing oil pump gear
- 3.10 Removing idler gear
- 3.11 Removing PTO drive gear
- 3.12 Removing camshaft
- 3.13 Separating camshaft gear
- 3.14 Installing camshaft gear and thrust plate
- 3.15 Removing front plate
- 3.16 Removing oil pump
- 4. Disassembling and inspecting piston, connecting rod, crankshaft and crankcase
- 4.1 Removing connecting rod cap
- 4.2 Removing carbon deposits from the upper part of cylinder liner
- 4.3 Pulling out piston
- 4.4 Removing piston ring
- 4.5 Removing piston pin and piston
- 4.6 Removing main bearing cap
- 4.7 Removing crankshaft
- 4.8 Removing tappet
- INSPECTION AND REPAIR OF BASIC ENGINE
- 1. Inspecting and repairing cylinder head and valve mechanism
- 1.1 Measuring clearance between rocker bushing and rocker shaft
- 1.2 Measuring valve stem outside diameter and valve guide inside diameter
- 1.3 Replacing valve guide
- 1.4 Inspecting valve face
- 1.5 Refacing valve face
- 1.6 Refacing valve seat
- 1.7 Replacing valve seat
- 1.8 Lapping valve and valve seat
- 1.9 Measuring perpendicularity and free length of valve spring
- 1.10 Measuring distortion of the bottom surface of the cylinder head
- 1.11 Measuring push rod runout
- 1.12 Removing combustion jet
- 2. Inspecting and repairing flywheel
- 2.1 Measuring flatness of flywheel
- 2.2 Measuring flywheel face and radial runouts
- 2.3 Inspecting ring gear
- 2.4 Replacing ring gear
- 2.4.1 Removing ring gear
- 2.4.2 Installing ring gear
- 3. Inspecting and repairing timing gear and camshaft
- 3.1 Measuring timing gear backlash
- 3.2 Measuring idler gear and camshaft gear end play
- 3.3 Measuring cam lift
- 3.4 Measuring camshaft runout
- 3.5 Measuring camshaft journal outside diameter
- 3.6 Measuring camshaft bushing inside diameter
- 3.7 Replacing camshaft bushing
- 3.7.1 Removing camshaft bushing
- 3.7.2 Installing camshaft bushing
- 3.8 Measuring idler bushing inside diameter and idler shaft outside diameter
- 3.9 Replacing idler shaft
- 3.10 Measuring clearance between tappet and tappet guide hole
- 3.11 Inspecting tappet
- 3.11.1 Contact surface of camshaft
- 3.11.2 Contact surface of push rod
- 3.12 Inspecting V-belt groove wear
- 3.13 Inspecting damper
- 4. Inspecting and repairing piston, connecting rod, crankshaft and crankcase
- 4.1 Measuring crankcase top surface distortion
- 4.2 Measuring cylinder inside diameter
- 4.3 Measuring piston outside diameter
- 4.4 Measuring piston ring end gap
- 4.5 Measuring clearance between piston ring groove and piston ring
- 4.6 Measuring piston pin bore diameter and piston pin outside diameter
- 4.7 Measuring piston protrusion
- 4.8 Measuring clearance between connecting rod bearing and crankpin
- 4.9 Measuring clearance between connecting rod bushing and piston pin
- 4.10 Replacing connecting rod bushing
- 4.11 Inspecting connecting rod bend and twist
- 4.12 Inspecting connecting rod bearing
- 4.13 Measuring connecting rod end play
- 4.14 Weight difference of connecting rod assembly in one engine
- 4.15 Measuring crankshaft journal outside diameter
- 4.16 Measuring crankshaft crankpin outside diameter
- 4.17 Grinding crankshaft
- 4.18 Measuring crankshaft end play
- 4.19 Measuring crankshaft runout
- 4.20 Replacing crankshaft gear
- 4.20.1 Removing crankshaft gear
- 4.20.2 Installing crankshaft gear
- 4.21 Inspecting oil seal contact surface
- 4.22 Installing oil seal sleeve
- 4.23 Removing oil seal sleeve
- 4.24 Inspecting main bearing surface
- 4.25 Measuring clearance between main bearing and crankshaft journal
- REASSEMBLY OF BASIC ENGINE
- 1. Reassembling piston, connecting rod, crankshaft and crankcase
- 1.1 Installing main bearing
- 1.2 Installing thrust plate
- 1.3 Installing tappet
- 1.4 Installing crankshaft
- 1.5 Installing main bearing caps
- 1.6 Inserting side seal
- 1.7 Installing main bearing cap bolt
- 1.8 Measuring crankshaft end play
- 1.9 Reassembling piston and connecting rod
- 1.10 Installing piston ring
- 1.11 Preparation for installing pistons
- 1.12 Installing connecting rod bolt and connecting rod bearing
- 1.13 Installing pistons
- 1.14 Installing connecting rod cap
- 2. Reassembling timing gear and camshaft
- 2.1 Installing oil pump
- 2.2 Installing front plate
- 2.3 Installing camshaft gear and thrust plate
- 2.4 Installing camshaft
- 2.5 Installing PTO drive gear
- 2.6 Installing idler gear
- 2.7 Installing oil pump gear
- 2.8 Installing fuel injection pump
- 2.9 Inspecting and adjusting timing gear after installation
- 2.9.1 Inspecting backlash and end play
- 2.10 Installing front oil seal
- 2.11 Installing timing gear case
- 2.12 Installing oil strainer
- 2.13 Installing oil pan
- 2.14 Installing cover
- 2.15 Installing crankshaft pulley and damper
- 3. Reassembling flywheel
- 3.1 Installing oil seal
- 3.2 Installing rear plate
- 3.3 Installing flywheel
- 4. Reassembling cylinder head and valve mechanism
- 4.1 Cleaning cylinder head bottom surface
- 4.2 Installing valve stem seal
- 4.3 Installing valve and valve spring
- 4.4 Installing cylinder head gasket
- 4.5 Installing cylinder head assembly
- 4.6 Tightening cylinder head bolts
- 4.7 Inserting push rod
- 4.8 Reassembling rocker shaft assembly
- 4.9 Installing rocker shaft assembly
- 4.10 Determining top dead center of No. 1 cylinder compression stroke
- 4.10.1 When reusing the damper
- 4.10.2 When replacing the damper with a new one
- 4.11 Adjusting valve clearance
- 4.12 Installing rocker cover
- FUEL SYSTEM
- 1. Removing fuel system
- 1.1 Removing fuel filter
- 1.2 Removing fuel injection pipe
- 1.3 Removing fuel injection pump
- 2. Disassembling, inspecting and reassembling fuel system
- 2.1 Disassembling and inspecting fuel filter
- 2.2 Changing fuel filter
- 2.3 Disassembling and inspecting fuel injection nozzle
- 2.4 Inspecting and adjusting fuel injection valve opening pressure
- 2.5 Inspecting fuel spray pattern of fuel injection nozzle
- 2.6 Cleaning and inspecting nozzle tip
- 2.7 Reassembling fuel injection nozzle
- 2.8 Inspecting and cleaning gauze filter of distribute type fuel injection pump
- 3. Installing fuel system
- 3.1 Installing fuel injection pump
- 3.2 Installing fuel injection pipe
- 3.3 Installing fuel filter
- LUBRICATION SYSTEM
- 1. Removing lubrication system
- 1.1 Removing oil filter and relief valve
- 1.2 Removing oil cooler
- 1.3 Removing oil pump, oil pan and oil strainer
- 2. Disassembling, inspecting and reassembling lubrication system
- 2.1 Disassembling and inspecting oil pump
- 2.2 Inspecting oil pump
- 2.2.1 Measuring clearance between outer rotor and inner rotor
- 2.2.2 Measuring end play of rotor and pump case
- 2.2.3 Measuring clearance between outer rotor and pump case
- 2.2.4 Measuring clearance between main shaft and pump case
- 2.2.5 Measuring clearance between main shaft and bushing
- 2.2.6 Installing oil pump bushing
- 2.3 Reassembling oil pump
- 2.4 Disassembling and inspecting oil cooler
- 2.5 Inspecting oil filter
- 2.6 Inspecting relief valve
- 2.7 Inspecting safety valve
- 3. Installing lubrication system
- 3.1 Installing oil pump, oil pan and oil strainer
- 3.2 Installing oil cooler
- 3.3 Installing oil filter and relief valve
- COOLING SYSTEM
- 1. Removing cooling system
- 1.1 Removing thermostat
- 1.2 Removing water pump, water pump pulley and V-belt
- 2. Disassembling, inspecting and reassembling cooling system
- 2.1 Disassembling and inspecting thermostat
- 2.2 Inspecting thermostat
- 2.3 Disassembling water pump
- 2.4 Inspecting water pump
- 3. Installing cooling system
- 3.1 Installing water pump, water pump pulley and V-belt
- 3.2 Installing thermostat
- INLET AND EXHAUST SYSTEMS
- 1. Removing turbocharger, inlet and exhaust systems
- 1.1 Removing turbocharger
- 1.2 Removing inlet manifold
- 1.3 Removing exhaust manifold
- 2. Disassembling, inspecting and reassembling inlet and exhaust systems
- 2.1 Measuring exhaust manifold distortion
- 2.2 Disassembling and inspecting turbocharger
- 2.2.1 Removing turbine housing
- 2.2.2 Removing compressor cover
- 2.2.3 Installing O-ring
- 2.2.4 Installing compressor cover
- 2.2.5 Installing snap ring
- 2.3 Cleaning
- 2.3.1 Measuring axial clearance of cartridge assembly
- 2.3.2 Reassembling turbocharger
- 2.3.3 Installing turbine housing
- 2.3.4 Installing coupling assembly
- 3. Installing turbocharger, inlet and exhaust systems
- 3.1 Installing exhaust manifold
- 3.2 Installing inlet manifold
- 3.3 Installing turbocharger
- ELECTRICAL SYSTEM
- 1. Removing electrical system
- 1.1 Removing starter
- 1.2 Inspection before removing alternator
- 1.2.1 Inspecting alternator operation
- 1.2.2 Handling precaution
- 1.3 Removing alternator
- 1.4 Removing glow plug
- 2. Disassembling, inspecting and reassembling electrical system
- 2.1 Inspection before disassembling starter
- 2.1.1 Inspecting magnetic switch
- 2.1.2 No load test
- 2.2 Disassembling and inspecting starter
- 2.2.1 Removing pinion set
- 2.2.2 Removing magnetic switch
- 2.2.3 Removing rear bracket
- 2.2.4 Removing brush holder and brush assembly
- 2.2.5 Removing armature and yoke
- 2.2.6 Removing overrunning clutch
- 2.3 Inspecting and repairing starter
- 2.3.1 Inspecting brushes for wear
- 2.3.2 Measuring brush spring load
- 2.3.3 Inspecting brush holder for insulation
- 2.3.4 Measuring commutator radial runout
- 2.3.5 Measuring commutator outside diameter
- 2.3.6 Measuring undercut depth
- 2.3.7 Checking armature coil
- 2.3.8 Inspecting field coil
- 2.3.9 Inspecting rear bracket
- 2.3.10 Inspecting overrunning clutch operation
- 2.3.11 Inspecting front bracket
- 2.3.12 Inspecting gears of starter
- 2.3.13 Inspecting magnetic switch
- 2.3.14 Inspecting starter relay
- 2.4 Reassembling starter
- 2.4.1 Installing gear shaft
- 2.5 Disassembling and inspecting alternator
- 2.5.1 Separating front bracket from stator
- 2.5.2 Removing field coil
- 2.5.3 Removing pulley
- 2.5.4 Removing rear bearing
- 2.5.5 Removing front bearing
- 2.5.6 Removing stator
- 2.5.7 Removing regulator assembly
- 2.5.8 Removing rectifier assembly
- 2.6 Inspecting and repairing alternator
- 2.6.1 Inspecting stator
- 2.6.2 Inspecting rectifier
- 2.6.3 Measuring field coil
- 2.7 Reassembling alternator
- 2.7.1 Installing rectifier assembly and regulator assembly
- 2.7.2 Installing stator
- 2.7.3 Installing front bearing
- 2.7.4 Installing rear bearing
- 2.7.5 Installing pulley
- 2.7.6 Assembling stator and front bracket
- 2.8 Inspecting glow plug
- 2.8.1 Continuity test of glow plug
- 2.8.2 Heating test of glow plug
- 2.9 Inspecting magnetic valve (stop solenoid)
- 2.9.1 Continuity test of magnetic valve (stop solenoid)
- 2.9.2 Inspecting magnetic valve (stop solenoid) operation
- 2.10 Installing magnetic valve (stop solenoid)
- 3. Installing electrical system
- 3.1 Installing glow plug
- 3.2 Installing alternator
- 3.3 Installing starter
- ADJUSTMENT AND OPERATION
- 1. Adjusting engine
- 1.1 Inspecting and adjusting valve clearance
- 1.1.1 Inspecting valve clearance
- 1.1.2 Adjusting valve clearance
- 1.2 Draining fuel system
- 1.2.1 Draining fuel filter
- 1.3 Bleeding fuel system
- 1.3.1 Bleeding fuel filter
- 1.4 Inspecting and adjusting fuel injection timing
- 1.4.1 Adjusting fuel injection timing
- 1.5 Inspecting V-belt and adjusting V-belt tension
- 1.6 Inspecting V-belt
- 1.7 Adjusting V-belt tension
- 2. Break-in operation
- 2.1 Starting up
- 2.2 Inspecting engine condition after starting up
- 2.3 Break-in operation time
- 2.4 Inspection and adjustment after break-in operation
- 3. Performance test (JIS standard)
- 3.1 Engine equipment condition
- 3.2 Test items and purposes
- 3.2.1 Operation load test
- 3.2.2 Continuous load test
- 3.2.3 Low idle test
- 3.3 Other inspections
- 3.4 Engine output adjustment
- 3.4.1 Standard atmospheric conditions:
- 3.4.2 Calculation of corrected power
OPERATORS MANUAL
- FOREWORD
- SECTION 1
- SAFETY HINT
- Group 1 Before operating the machine
- Group 2 During operating the machine
- Group 3 During maintenance
- Group 4 Parking
- SECTION 2
- SPECIFICATIONS
- Group 1 Major components
- Group 2 Specifications
- Group 3 Working range
- Group 4 Weight
- Group 5 Lifting capacities
- Group 6 Bucket selection guide
- Group 7 Undercarriage
- Group 8 Specification for major components
- Group 9 Recommended oils
- SECTION 3
- CONTROL DEVICE
- Group 1 Cab device
- Group 2 Cluster
- Group 3 Switches
- Group 4 Levers and pedals
- Group 5 Air conditioner and heater
- Group 6 Others
- SECTION 4
- OPERATION
- Group 1 Suggestion for new machine
- Group 2 Check before starting the engine
- Group 3 Starting and stop the engine
- Group 4 Mode selection system
- Group 5 Operation of the working device
- Group 6 Traveling of the machine
- Group 7 Efficient working method
- Group 8 Operation in the special work sites
- Group 9 Normal operation of excavator
- Group 10 Attachment lowering Pattern
- Group 11 Storage
- Group 12 RCV lever operating pattern
- Group 13 Switching Hydraulic attachment circuit
- SECTION 5
- TRANSPORTATION
- Group 1 Preparation for transportation
- Group 2 Dimension and weight
- Group 3 Loading the machine
- Group 4 Fixing the machine
- Group 5 Loading and unloading by crane
- SECTION 6
- MAINTENANCE
- Group 1 Instructions
- Group 2 Tightening torque
- Group 3 Specification of fuel, coolant and lubricants
- Group 4 Maintenance check list
- Group 5 Maintenance chart
- Group 6 Service instruction
- Group 7 Electrical system
- Group 8 Air conditioner and heater
- SECTION 7
- TROUBLESHOOTING GUIDE
- Group 1 Engine
- Group 2 Electrical system
- Group 3 Others
- SECTION 8
- HYDRAULIC BREAKER
- Group 1 Selecting hydraulic breaker
- Group 2 Circuit configuration
- Group 3 Maintenance
- Group 4 Precaution while operating the breaker
- Group 5 Quick clamp
- INDEX