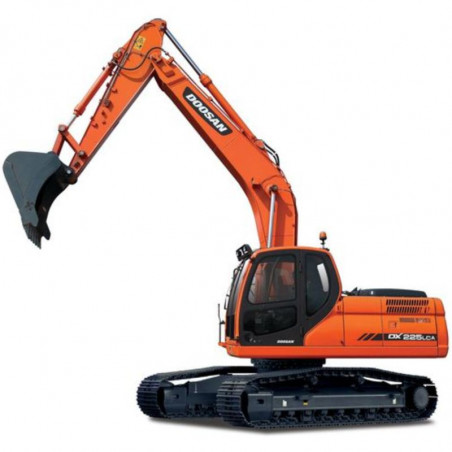
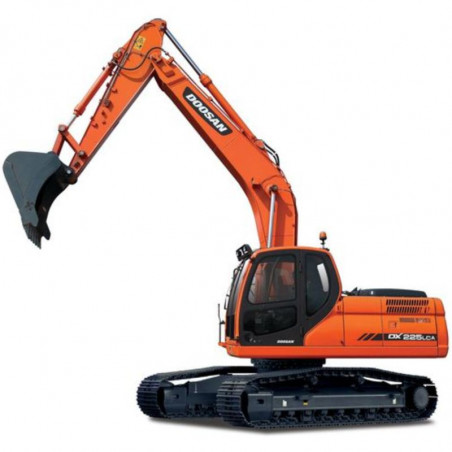
DOOSAN DX225LCA - WORKSHOP, SERVICE, REPAIR MANUAL - WIRING DIAGRAMS
- English Service Manual and Wiring Diagrams, for Doosan DX225LCA.
CONTENTS:
Safety
- Track Excavator Safety
- Safety Precautions
- Applicable Models
- To the Operator of a DOOSAN Excavator
- Learn the Signal Words Used with the Safety Alert Symbol
- General Safety Essentials
- Accessory Applications
- Lifting Capacity Rating Configuration
- Location of Safety Labels
- Summary of Safety Precautions for Lifting in Digging Mode
- Unauthorized Modifications
- General Hazard Information
- Safety Rules
- Safety Features
- Inside Operator's Compartment
- Clothing and Personal Protective Items
- Breathing Masks, Ear Protection May Be Required
- Vibration Level Information
- Recommendations for Limiting Vibrations
- Mounting and Dismounting
- Fuel, Oil and Hydraulic Fluid Fire Hazards
- Precautions When Handling Fluids at High Temperature
- Asbestos Dust Hazard Prevention
- Injury from Work Equipment
- Fire Extinguisher and First Aid Kit
- Protection from Falling or Flying Objects
- Attachment Precautions
- Accumulator
- Indoor Ventilation
- Emergency Exit
- Before Starting Engine
- Work Site Precautions
- Checks Before Starting Engine
- Engine Starting
- Before Operating Machine
- Machine Operation
- When Swinging or Changing Direction of Travel
- Travel Precautions
- Traveling on Slopes
- Prohibited Operations
- Precautions for Operation
- Avoid High Voltage Cables
- Protecting Cabin from Falling Object (Optional)
- Operate Carefully on Snow, Ice and in Very Cold Temperatures
- Operations on Slopes
- Parking Machine
- Never Let Anyone Ride on Attachment
- Maintenance
- Warning Tag
- Clean Before Inspection or Maintenance
- Proper Tools
- Use of Lighting
- Fire Prevention and Explosion Prevention
- Burn Prevention
- Welding Repairs
- Warning for Counterweight and Front Attachment Removal
- Precautions for Removal, Installation, and Storage of Attachments
- Precautions When Working on Machine
- Lock Inspection Covers
- Crushing Prevention and Cutting Prevention
- Track Tension Adjustments Require Caution
- Supports and Blocking for Work Equipment
- Action When Abnormality Is Found During Inspection
- Precautions with High-pressure Lines, Tubes and Hoses
- Waste Materials
- Battery
- Battery Hazard Prevention
- Boost Starting or Charging Engine Batteries
- Towing
- Precautions When Towing
- Shipping and Transportation
- Obey State and Local Over-the-Road Regulations
- Lifting With Sling
Specifications
- Specification for DX225LCA
- Safety Precautions
- Applicable Models
- General Description
- Component Locations
- General Dimensions
- Working Range
- General Specifications
- Engine Performance Curves (Per DIN 6270 Standard)
- Approximate Weight of Workload Materials
- Performance Tests
- Excavator Performance Standards
- Test Conditions
- Travel Speed and Travel Motor Balance (Steering Deviation) Tests
- Speed Test
- Travel Deviation
- Swing Speed and Deceleration Force Test
- Swing Speed Test
- Swing Deceleration Force Test
- Cylinder Performance Tests
- Boom Cylinders Test
- Arm Cylinder Test
- Bucket Cylinder Test
- Hydraulic Cylinder Natural Drop Test
- Travel Motor Jack-up Test
General Maintenance
- General Maintenance Procedures
- Safety Precautions
- Applicable Models
- Welding Precautions and Guidelines
- Hydraulic System - General Precautions
- Maintenance Service and Repair Procedure
- General Precautions
- Hydraulic System Cleanliness and Oil Leaks
- Maintenance Precautions for Hydraulic System Service
- Oil Leakage Precautions
- Cleaning and Inspection
- General Guidelines
- Bearing Inspection
- Normal Bearing
- Bent Cage
- Galling
- Abrasive Step Wear
- Etching
- Misalignment
- Indentations
- Fatigue Spalling
- Brinelling
- Cage Wear
- Abrasive Roller Wear
- Cracked Inner Race
- Smears
- Frettage
- Heat Discoloration
- Stain Discoloration
- Standard Torques
- Safety Precautions
- Applicable Models
- Torque Values for Standard Metric Fasteners
- Torque Values for Standard U.S. Fasteners
- Type 8 Phosphate Coated Hardware
- Torque Values for Hose Clamps
- Torque Values for Split Flanges
- Torque Wrench Extension Tools
- Torque Multiplication
- Other Uses for Torque Wrench Extension Tools
- Tightening Torque Specifications (Metric)
- I. "Loctite" Fastener Adhesives
- II. "Loctite" Pipe Thread Sealant
- III. "Loctite" gasket/flange sealer
- IV. "Loctite" retaining compounds
- V. "Loctite" Adhesives
Upper Structure
- Cabin
- Safety Precautions
- Applicable Models
- Removal
- Installation
- Counterweight
- Safety Precautions
- Applicable Models
- General
- Warning for Counterweight and Front Attachment Removal
- Removal
- Installation
- Fuel Tank
- Safety Precautions
- Applicable Models
- General Description
- Parts List
- Specifications
- Removal
- Installation
- Start-up Procedures
- Fuel Transfer Pump
- Safety Precautions
- Applicable Models
- General Description
- Theory of Operation
- Troubleshooting
- Replacement of Rotor and Vane
- Replacement of Rear Cover
- Replacement of Armature
- Swing Bearing
- Safety Precautions
- Applicable Models
- Swing Bearing Maintenance
- Operating Recommendation
- Measuring Swing Bearing Axial Play
- Measuring Bearing Lateral Play
- Swing Bearing Basic Operation
- Rebuilding Swing Bearing
- Swing Reduction Gear
- Safety Precautions
- Applicable Models
- General Description
- Theory of Operation
- Parts List
- Specifications
- Troubleshooting, Testing and Adjustment
- Removal
- Disassembly
- Cleaning and Inspection (Wear Limits and Tolerances)
- Reassembly
- Shaft and S/R Bearing Heat fit
- Assembly of Carrier Subassemblies
- Cleaning Carrier
- Cleaning Planet Gear
- Assembly of No. 1 Carrier
- Assembly of No. 2 Carrier
- Assembly of Main Case
- Cleaning Casing and Other Parts
- Assembly of Shaft and Pinion
- Assembly of Seal and Bearing
- Assembly of Ring Gear
- Assembly of Carrier.
- Assembly of the Motor
- Installation
- Start up Procedures
Lower Structure and Chassis
- Track Assembly
- Safety Precautions
- Applicable Models
- General Description
- Track Tension
- Cleaning and Inspection (Wear Limits and Tolerances)
- Track Shoe
- Lower Roller
- Upper Roller
- Front Idler
- Track Shoes and Links
- Track Removal
- Track Installation
- Front Idler Roller
- Parts List
- Front Idler Roller Disassembly
- Front Idler Roller Reassembly
- Lower Roller
- Parts List
- Lower Roller Removal
- Lower Roller Disassembly
- Lower Roller Reassembly
- Lower Roller Installation
- Upper Roller
- Parts List
- Upper Roller Removal
- Upper Roller Disassembly
- Upper Roller Reassembly
- Track Spring and Track Adjusting Cylinder
- Parts List
Engine and Drive Train
- Drive Coupling (Main Pump)
- Safety Precautions
- Applicable Models
- Drive Coupling
- Special Tools
- Installation of Drive Coupling
- Installation Procedure
Hydraulics
- Hydraulic System Troubleshooting, Testing and Adjustment
- Safety Precautions
- Applicable Models
- Hydraulic System - General Notes
- Hydraulic Schematic
- General Notes
- Operation of Working Components
- Boom Operating Circuit
- Boom Up Circuit
- Boom Down Circuit
- Arm Operating Circuit
- Arm Crowd Circuit
- Arm Dump Circuit
- Bucket Operating Circuit
- Bucket Crowd Circuit
- Bucket Dump Circuit
- Swing Operating Circuit
- Right Swing Operating Circuit
- Left Swing Operating Circuit
- Swing Relief Valve and Makeup Valve
- Travel Operating Circuit
- Forward Travel Circuit
- Reverse Travel Circuit
- Procedural Troubleshooting Baseline Recommendations
- Initial Checks and Tests to Establish Operating Condition of the Excavator
- Triage Summary
- Pilot Pressure
- Adjustment and Testing
- Power Mode Valve
- Current Signal and Hydraulic Pressure Adjustments
- Swing Priority Valve
- Control Valve Pressure and Current Adjustments
- Pressure Up Valve
- Checks and Adjustments
- Pump Input Power Control
- Pump Regulator Adjustment
- Flow Meter and Flow Meter Kit Installation and Testing
- Installation and Testing Procedure
- Swing System Troubleshooting
- Precautions/Initial Checks
- Swing Relief Valve Checking and Adjustment
- Troubleshooting – Swing Gearbox
- Troubleshooting – Hydraulic Problems
- Troubleshooting – Control Valve
- Troubleshooting – Travel Control Valve
- Troubleshooting – Joystick Control Valve
- Accumulator
- Safety Precautions
- Applicable Models
- General Description
- Specifications
- Center Joint (Swivel)
- Safety Precautions
- Applicable Models
- General Description
- Parts List
- Troubleshooting, Testing and Adjustment
- Inspection
- Testing
- Disassembly
- Reassembly
- Cylinders
- Safety Precautions
- Applicable Models
- General Description
- Theory of Operation
- Parts List
- Special Tools and Materials
- Piston Nut
- Piston Jig
- Steel Bushing Jig
- Dust Wiper Jig
- Slipper Seal Jig
- Slipper Seal Straightening Jig
- Disassembly
- Reassembly
- Swing Motor
- Safety Precautions
- Applicable Models
- Operation Manual
- Information on Marking
- Specifications
- Structure and Operational Principles
- Structure
- Operational Principles
- Brake Subassembly
- Cautions
- Check Points
- Rotation Direction
- External Load on Shaft End
- Active Oil and Temperature Range
- Filter
- Installation and Piping
- Fillup and Air Discharge
- Cautions During Start
- Causes and Solutions of Problems
- General Cautions.
- How to Check Defects of Motor
- Symptoms and Solutions of Problems
- Maintenance Instructions
- Disassembly and Assembly
- Bolt Tightening Torque
- Tools Used for Disassembly and Assembly
- Disassembly
- Assembly
- Maintenance
- References for Replacement of Worn Parts
- Fixing References for Sliding Parts
- Travel Motor
- Safety Precautions
- Applicable Models
- TM40VD Operation Manual
- General Specifications
- Legend
- Basic Structure and Diagram
- Basic Structure of TM Motor
- Operation Principles
- Reducer
- Hydraulic Motor (Brake Valve, Parking Brake, High and Low 2-Speed Shifting)
- Cautions in Use
- Fitting (Refer to the External Specifications Diagrams.)
- Piping
- Hydraulic Oil
- Lubricating Oil
- Maintenance
- Troubleshooting
- External Specifications Diagrams
- Basic Structure and Diagrams
- Assembly Cross Section
- Parts List
- TM40VD Maintenance Instructions
- Precautions
- Tools List for Disassembly and Reassembly
- Standard Tools
- Machined Tools
- Disassembly Instructions
- General Cautions
- Disassembly procedure
- Disassembling Hydraulic motor Part
- Reassembly
- General Precautions
- Reassembly Procedure
- Reassemble the Hydraulic Motor Part
- Reassemble the Rear Flange Part (1)
- The Reduction Gear Assembly
- Checking Facts After Assembly
- Testing
- List of Seals
- Gear Pump
- Safety Precautions
- Applicable Models
- Single Gear Pump
- Disassembly
- Reassembly
- Main Control Valve
- Safety Precautions
- Applicable Models
- General Description
- Theory of Operation
- When All Spools are in Neutral
- Single Operation
- Compound Operation
- Antidrift Valve
- Main Relief Valve
- Overload Relief Valve
- Low-pressure Relief Valve
- Parts List
- Specifications
- Troubleshooting, Testing and Adjustment
- Troubleshooting
- Overall Control Valve
- Relief Valve
- Overall Oil Pressure
- Adjustment of Valves
- Main Relief Valve
- Overload Relief Valve
- Disassembly
- Caution in Disassembly
- Disassembly of Main Spool Part
- Disassembly of Arm 1 Para-turn Spool Part
- Disassembly of Arm Regeneration Release Valve Part
- Disassembly of Load Check Valve Part
- Disassembly of Antidrift Valve Part
- Disassembly of Relief Valve
- Disassembly of Option Section Part
- Disassembly of Other Plugs
- Disassembly of Valve Housing Bolt
- Disassembly of Main Relief Valve
- Disassembly of Overload Relief Valve
- Instruction of Disassembly and Assembly of Low-pressure Relief Valve
- Cleaning and Inspection (Wear Limits and Tolerances)
- Cleaning
- Inspection
- Reassembly
- Caution on Assembly
- Caution on Handling O-ring
- Caution on Handling Spool
- Method of Painting the Adhesives (screw part and arm screw part of parts requiring the adhesiveness)
- Sequence of Subassembly
- Spool Assembly (Main Spool)
- Arm 1 Para-turn Spool Assembly
- Antidrift Valve Assembly
- Assembly Sequence of Main Body of the Control Valve
- Assembly of Relief Valve
- Assembly of Load Check Valve
- Assembly of Antidrift Valve
- Assembly of Option Section Part
- Assembly of Arm Regeneration Release Valve
- Assembly of Arm 1 Para-turn Spool
- Assembly of Main Spool
- Assembly of Other Plugs
- Maintenance of Relief Valves
- Reassembly of Main Relief Valve
- Reassembly of Overload Relief Valve (69, Total of 6 Places)
- Reassembly of Low-pressure Relief Valve (70, Total of 2 Places)
- Installation
- Start-up Procedures
- Axial Piston Pump
- Safety Precautions
- Applicable Models
- Pump Maintenance
- Component Locations
- Parts List
- Tools
- Tightening Torque
- Disassembly
- Reassembly
- Pump Body Maintenance Standards
- Change Standards of Worn Parts
- Fix Standards of Cylinder Block, Valve Plate, and Swash Plate (Shoe Plate)
- PTO Server
- Safety Precautions
- Applicable Models
- Pump Maintenance
- Disassembly
- Reassembly
- Maintenance Standards of Pump Body
- Remote Control Valve (Work Lever / Joystick)
- Safety Precautions
- Applicable Models
- General Description
- Theory of Operation
- Structure
- Function
- Parts List
- Specifications
- Performance
- Torques
- Tools and Materials
- Disassembly
- Cleaning and Inspection (Wear Limits and Tolerances)
- Reassembly
- Start-up Procedures
- Travel Control Valve (with Damper)
- Safety Precautions
- Applicable Models
- General Description
- Theory of Operation
- Pressure Reducing Valve
- Operating Theory of Damper Mechanism
- Causes of Faults and Measures
- Parts List
- Specification
- Torques
- Removal
- Disassembly
- Cleaning and Inspection (Wear Limits and Tolerances)
- Reassembly
- Installation
- Start up Procedures
- Solenoid Valve Assembly
- Safety Precautions
- Applicable Models
- 5-Solenoid Valve
- Parts List
- Functions of 5-Solenoid Valve Assembly Package
- This solenoid valve assembly package have the following functions.
- Functions and Operations of Solenoid Valves
- Detailed Functions and Operations of Solenoid Valves
- Assembly Diagram and Tools Required
- Cautions During Disassembly and Reassembly
- Solenoid Valve Diagram
- Check Points and Solutions for Problems
- Checking of Pilot Pressure for Defects
- 2-Solenoid Valve
- Parts List
- Assembly Diagram and Tools Reguired
- Cautions During Disassembly and Reassembly
- Solenoid Valve Diagram
- Troubleshooting Guide
- Breaker EPPR Valve (Opt)
- Safety Precautions
- Applicable Models
- Structure
- Numbers and Names of Parts
- Functions and Operation
- Cautions for Operation
- Maintenance Instructions
- Maintenance
- Bolt Tightening Torque
- Tools Used for Disassembly and Assembly
- Disassembly
- Assembly
- Hydraulic Schematic (DX225LC/ DX225LCA)
- Safety Precautions
- Applicable Models
- DX225LC/DX225LCA
Electrical System
- Electrical System
- Safety Precautions
- Applicable Models
- Introduction
- Electric Wire Color
- Electrical Supply System
- Engine Starting Circuit
- Start Operation
- After Start
- Operation of the Start Circuit (2) Immediately After Start
- Engine Preheating System
- Engine Stop
- Charging System
- Monitoring System
- Instrument Panel
- Monitoring System Schematic
- Operation
- Instruments
- Warning and Indicator Lights
- Indication of Warning Lights
- Indication of Multifunction Gauge and Letter Information Area
- Initial Operation
- Mode Selector Switch
- Power Mode Switch
- Auto Idle Switch
- Graphic Information Area Display
- Overview
- Main Menus for the Graphic Display Area
- Menu Selector Buttons
- Main Menu
- Language
- Set Clock
- Filter/Oil Info
- Menu Display Order and Icon Explanation
- Adjust Display
- Set Password
- Special Menu
- Entering/Accessing and Exiting/Escaping Menus
- Entering/Accessing Menus
- Exiting/Escaping Menus
- Special Menu Selections
- Information of Machine Status
- Failure Information
- Information of Machine Operation
- Machine Operation Info Screen
- Electronic Hydraulic Control System (e EPOS)
- Control System Schematic
- Power Mode Control
- Operation
- 1. Power Mode
- 2. Standard Mode
- 3 Operation in case of failure in the control system (Aux mode operation
- Power Mode Control Circuit Diagram
- Work Mode Control
- Work Mode Control Circuit Diagram
- Engine Control System
- Engine Control Dial
- Engine Control Motor
- Engine Control Circuit Diagram
- Automatic Deceleration Control (Auto Idle Control)
- Engine Overheat Protection System
- Power Boost Mode
- Operation
- Power Boost Control Circuit Diagram
- Automatic Travel Speed Control
- Automatic Travel Speed Control Circuit Diagram
- Adjust Engine Speed
- Engine Throttle controller
- Self diagnostic Function
- e EPOS Controller
- Air Conditioner System
- Outline
- Internal and External Filters
- How to Check Internal Air Filter
- How to Check External Air Filter
- Air Conditioning System Layout
- Air Conditioner/heater Circuit Diagram
- Air Conditioner/heater Unit
- Air Flow Diagram
- Door Open by Vent Modes
- Main Components
- Actuator Wind Direction Control
- Actuator Temperature Control
- Actuator Internal/external Air Exchange
- Air Flow Control Module
- Ambient Air Temperature Sensor
- Sun Sensor
- Control Panel
- Appearance and Terminal Arrangement
- Terminal Terms
- Control Logic
- Self Diagnosis
- Ambient Temperature Display
- Compressor
- Receiver Dryer
- Wiper System
- Wiper Circuit
- Wiper operation
- Continuous operation
- Intermittent operation
- Lighting System
- Lighting System Circuit Diagram
- Kind of Light
- Operation
- Overload Warning Device
- Overload Warning Device Circuit Diagram
- Audio Controller
- Audio Controller Circuit Diagram
- Operations Via Audio Control Panel
- Electrical Schematic (DX225LCA)
- Safety Precautions
- Applicable Models
- DX225LCA
Attachments
- Boom and Arm
- Safety Precautions
- Applicable Models
- Front Attachment Pin Specifications
- Front Attachment - Removal and Installation
- Arm Removal Procedure
- Boom Removal Procedure
- Installation
- Arm Installation Procedure
- Boom Installation Procedure
- Start-up Procedures
- Bucket
- Safety Precautions
- Applicable Models
- Bucket Tooth Inspection and Replacement
- Bucket O-ring Replacement
- Bucket Attachment, Removal and Reversal
- Detaching the Bucket
- Attaching the Bucket
- Reversing the Bucket