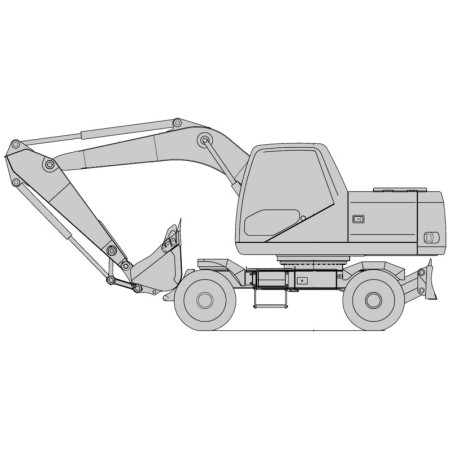
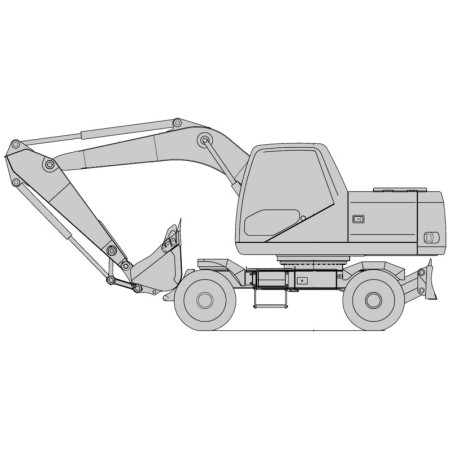
DAEWOO SOLAR S170W-V EXCAVATOR - WORKSHOP, SERVICE, REPAIR MANUAL
- English Service Manual, to excavator Daewoo Solar S170W-V.
CONTENTS:
SAFETY
Wheel Excavator Safety S0102020
- To the Operator of a Daewoo Excavator
- Learn the Signal Words Used with the Safety Alert Symbol
- General Safety Essentials
- Accessory Applications
- Lifting Capacity Rating Configuration
- Location of Safety Labels
- Summary of Safety Precautions for Lifting in Digging Mode
- Unauthorized Modifications
- Work-site Precautions
- Attachment Precautions
- Avoid High-voltage Cables
- Before Starting to Dig, Contact Authorities
- Be Aware of Height Obstacles
- Use Care on Loose Support
- Use Solid Support Blocking
- Overhangs Are Dangerous
- Sloping Terrain Requires Caution
- Stay Alert for People Moving through the Work Area
- Be Aware of and Conform to Local Regulations
- Operation
- Operate While Seated at the Operator’s Station ONLY
- Before Starting the Engine
- Never Use Ether Starting Aids
- Mounting and Dismounting
- Observe General Safety Rules
- Engine Ventilation
- Asbestos Dust Hazard Prevention
- Take Time to Provide Good Visibility
- Fuel, Oil and Hydraulic Fluid Fire Hazards
- Boost Starting or Charging Engine Batteries
- Travel Controls May Produce Reversed Operations
- Keep "Pinch Point" Areas Clear - Use Caution in Reverse and Swing
- Travel Precautions
- Operate Carefully on Snow and Ice and in Very Cold Temperatures
- Parking the Machine
- Shutdown Control Functions
- Equipment
- Rough Operation May Require Use of Certified Safety Equipment
- Install Additional Safety Equipment If Conditions Require
- Movement Alarms
- Seat Belts Should Be Used at All Times
- Window Glass Breaking Tool
- Keep a Fire Extinguisher at Hand
- Maintain Standard Safety Equipment in Good Condition
- Safety-critical Parts Must Be Replaced Periodically
- Hydraulic Cylinder Seals Require Periodic Replacement
- High Pressure Hydraulic Lines Can Store a Great Deal of Energy
- The Operator’s Cab and Turntable Deck Should Be Kept Clean
- Wear Eye Protection and Safety Clothing
- Breathing Masks, Ear Protection May Be Required
- Battery Electrolyte and Explosive Gases Can Be Lethal
- Disconnect Batteries for Electrical Service Before Electrical Welding
- Use Low Heat Portable Lighting
- Maintenance
- Use Warning Tag Control Lockout Procedures During Service
- Do not Run the Engine If Repairs or Work Is Being Performed Alone
- Always Use Adequate Equipment Supports and Blocking
- Do not Work on Hot Engines or Hot Cooling or Hydraulic Systems
- Cool-down Is Required Prior to Radiator or Reservoir Checks
- Pressurized Hydraulic Oil Fluid Leaks Can Be Dangerous
- Obtain immediate medical attention if pressurized oil pierces the skin
- Use Correct Replacement Fasteners Tightened to Proper Torque
- Dispose of All Petroleum-based Oils and Fluids Properly
- Shipping and Transportation
- Obey State and Local Over-the-Road Regulations
SPECIFICATIONS
Specifications for Solar 170W-V S0202060
- General Description
- Component Location
- General Dimensions
- Dimensions
- Working Range
- Hydraulic Cylinders
- Engine Specifications
- Engine Performance Curves (Per KS R1004 Standard)
- Approximate Weight of Workload Materials
- General Specifications
- Hydraulic System Component Specifications
- System Component Specifications
- Drive System
- Swing Mechanism
- Brake System
- Steering System
- Chocking System
- Performance Tests and Standards
- Standards
- Tests
- Test Conditions
- Travel Speed Tests
- Swing Speed Test
- Swing Speed Test
- Swing Force Test
- Cylinder Performance Tests
- Boom Cylinders Test
- Arm Cylinder Test
- Bucket Cylinder Test
- Hydraulic Cylinder Natural Drop Test
GENERAL MAINTENANCE
General Maintenance Procedures S0302000
- Welding Precautions and Guidelines
- Hydraulic System - General Precautions
- Maintenance Service and Repair Procedure
- General Precautions
- Hydraulic System Cleanliness and Oil Leaks
- Maintenance Precautions for Hydraulic System Service
- Oil Leakage Precautions
- Cleaning and Inspection
- General Guidelines
- Bearing inspection
Standard Torques S0309000
- Torque Values for Standard Metric Fasteners
- Torque Values for Standard U.S. Fasteners
- Type 8 Phosphate Coated Hardware
- Torque Values for Hose Clamps
- Torque Values for Split Flanges
- Torque Wrench Extension Tools
- Torque Multiplication
- Other Uses for Torque Wrench Extension Tools
- Tightening Torque Specifications (Metric)
UPPER STRUCTURE
Cab S0402020
- Removal
- Installation
- Window and Gasket Replacement
- Falling Object Protective Structures (F.O.P.S.)
Counterweight S0403000
- General
- Removal
- Installation
Fuel Tank S0405100
- General Description
- Parts List
- Specifications
- Removal
- Installation
- Start-up Procedures
Fuel Transfer Pump S0405500
- General Description
- Theory of Operation
- Replacement of Rotor and Vane
- Replacement of Rear Cover
- Replacement of Amateur
Swing Bearing S0407010
- Swing Bearing Maintenance
- Operating Recommendation
- Measuring Swing Bearing Axial Play
- Measuring Bearing Lateral Play
- Swing Bearing Basic Operation
- Rebuilding Swing Bearing
Swing Reduction Gearbox S0408050
- General Description
- Theory of Operation
- Parts List
- Specifications
- Special Tools and Materials
- Special Tools
- Troubleshooting, Testing and Adjustment
- Removal
- Disassembly
- Cleaning and Inspection (Wear Limits and Tolerances)
- Reassembly
- Installation
LOWER STRUCTURE AND CHASSIS
Ram Lock Valve Operation S0503000
- Theory of Operation
ENGINE AND DRIVE TRAIN
Front Axle S0602120
- APL-B755
- Inscriptions On the Model Identification Plate (For Zf-axles)
- Examples of Gear-tooth Contact Patterns for the Gleason Gear-tooth System
- Lubrication and Maintenance Instructions
- Oil Quality
- Oil Change
- List of Lubricants TE-ML 05
- Brake Lining - Wear Test On Zf-axles of the Series AP (L) - B 700
- Carry Out Wear Test
- Dimension "X" - Dimension "Y" = Actual Value (Piston Stroke + Wear)
- Special Tools
- Final Drive - Disassembly
- Planetary Carrier
- Internal Gear
- Hub
- Steering Knuckle Hull
- Double-joint Shaft
- Axle Housing
- Final Drive - Reassembly
- Axle Housing and Double-joint Shaft
- Steering Knuckle Hull
- Adjusting Steering Knuckle Bearing
- Check Rolling Resistance of the Steering Knuckle Bearing
- Hub - Wheel Bearing
- Adjust and Check the Rolling Moment of the Wheel Bearing
- Internal Gear
- Multi-disk Brake
- Planetary Gears
- Illustrated Table
- Drive Unit/ Differential Disassembly
- Disassemble Differential
- Disassemble Differential
- Remove Drive Pinion
- Drive Unit/differential - Reassembly
- Determine Thickness of Shim - To Obtain A Correct Contact Pattern
- Install Drive Pinion
- Adjust Rolling Moment of the Drive Pinion Bearing
- Complete and Install Differential
- Determine and Adjust Backlash of the Crown
- Check Contact Pattern
- Only for Version - 100% Lock Install Shut-off Slide and Piston
- Axle Bolting
- Mount Final Drive
- Illustrated Tables
- Steering Assembly - Disassembly
- Remove Tie Rod
- Remove Piston and Cylinder
- Steering Assembly - Reassembly
- Install Guide, Cylinder and Piston
- Adjust Track and Steering Lock
- Illustrated Table
Rear Axle S0602130
- Examples of Gear-tooth-contact Patterns for the Gleason Gear-tooth System
- Ideals Tooth-contact Pattern I.E. Pinion Distance Is Correct
- Inscriptions on the Model Identification Plate (For ZF-axles)
- Lubrication and Maintenance Instructions
- Technical Data
- Adjustment Values Final Drive
- Drive Unit/differential
- Brake Lining Wearing Test
- Carry Out the Wearing Test
- Special Tools
- Final Drive (Planetary) Disassembly
- Loosen Slotted Nut
- Drive Unit - Differential Disassembly
- Remove Differential
- Dismantle Differential
- Remove Drive Pinion
- Cleaning and Inspection (Wear Limits and Tolerances)
- Drive Unit - Differential Reassembly
- Drive Pinon
- Complete and Install Differential
- Final Drive (Planetary) Reassembly
- Hub Carrier
- Hub
- Internal Gear
- Tighten Slotted Nut
- Multi-disk Brake
- Planetary Carrier
Service Brake S0603010
- Measuring Wear of Brake Disc
- Special Tool
- When to Measure Brake Disc Wear
- How to Measure Brake Disc Wear.
- Maximum Allowable Value of "X" - "Y"
Air-Conditioner S0605010
- General Description
- Refrigerant Circulation
- Control Panel
- Control Specifications
- Temperature Level Control and Display
- Air Discharge According to Path Selection
- Air-conditioning System Circuit Diagram
- Troubleshooting
- Weight of R134a Gas Used In Machines
- Refrigerant System Repairs
- Refrigerant Safe Handling Procedures
- Repair and Replacement Procedure
- Refrigerant Recovery
- Vacuuming Refrigerant System
- Leakage Check
- Refrigerant Charging
- Inspecting System For Leakage
Transmission (ZF 2HL 100) S0607050
- Transmission Design and Options
- Power Flow
- Transmission Design
- Shift Control
- Instructions for Starting, Operation and Maintenance
- Oil Capacity
- Admitted Oils
- Installation View and Instructions for the Oil Filling Procedure
- Gearbox and Axle
- Instructions for Moving the Vehicle or An Emergency Towing
- Examples of Gear-tooth-contact Patterns for the Gleason Gear-tooth System
- Disassembly
- Separate Gearbox From Axle
- Remove Shifting Clutches
- Remove and Dismantle Planetary Drive
- Remove and Dismantle Declutch Unit and Spur Gear
- Dismantle Shift Lock
- Disassemble Final Drive, Axle Carrier and Differential
- Reassembly
- Axle Carrier, Final Drive and Differential Version "A" - Gearbox Attached on the Axle
- Install Helical Gear and Declutch Unit
- Complete and Install Planetary Carrier
- Pre-assemble and Install Clutch (Road Gear)
- Install Brake (Cross-country Gear)
- Install Drive Casing
- Pre-assemble and Mount Shift Lock
- Pre-assemble and Install Control Spool
- Install Lubricating Oil Pump
- Mount Screw Plugs and Oil Lines
- Mount Gearbox on the ZF-axle
- Disassemble Final Drive
- Install Final Drive
Drive Coupling (Main Pump) S0609000
- Drive Coupling
- Special Tools
- Kawasaki Pump Tool
- Uchida Pump Tool
- Drive Coupling Installation
- Installation Procedure
HYDRAULICS
Hydraulic System Troubleshooting, Testing and Adjustment S0702150
- Hydraulic System - General Notes
- Operation of Working Components
- Boom Operating Circuit
- Boom Up Circuit
- Boom Down Circuit
- Arm Operating Circuit
- Arm Crowd Circuit
- Arm Dump Circuit
- Bucket Operating Circuit
- Bucket Crowd Circuit
- Bucket Dump Circuit
- Swing Operating Circuit
- Right Swing Operating Circuit
- Left Swing Operating Circuit
- Swing Relief Valve and Make-up Valve
- Procedural Troubleshooting Baseline Recommendations
- Initial Checks and Tests to Establish Operating Condition of the Excavator
- Pilot Pressure
- Adjustment and Testing
- Power Mode Valve
- Current Signal and Hydraulic Pressure Adjustments
- Boom/Swing Priority Valve
- Control Valve Pressure and Current Adjustments
- Pressure Up Valve
- Checks and Adjustments
- Pump Input Power Control
- Pump Regulator Adjustment
- Flow Meter and Flow Meter Kit Installation and Testing
- Swing System Troubleshooting
- Precautions/Initial Checks
- Swing Relief Valve Checking and Adjustment
- Troubleshooting - Swing Gearbox
- Troubleshooting - Hydraulic Problems
- Troubleshooting - Control Valve
- Troubleshooting - Joystick Control Valve
Accumulator S0703000
- General Description
- Specifications
- Accumulator Charging
- Charging the Accumulator with Nitrogen
Center Joint (Swivel) S0704070
- General Description
- Parts List
- Troubleshooting, Testing and Adjustment
- Inspection
- Testing
- Disassembly
- Reassembly
Cylinders S0705000
- General Description
- Theory of Operation
- Parts List
- Special Tools and Materials
- Piston Nut
- Piston Jig
- Disassembly
- Reassembly
Swing Motor S0707260
- General Description
- Theory of Operation
- Swing Motor Anti-cavitation Make-up Valve
- Relief Valve
- Swing Brake Operation
- Parts List
- Specifications
- Special Tools
- Disassembly
- Cleaning and Inspection (Wear Limits and Tolerances)
- Reassembly
Travel Motor S0707350
- General Description
- Theory of Operation
- Parts List
- Specifications
- Travel Motor General Disassembly and Reassembly Instructions
- Recommended Tools
- Precautions for Disassembly and Assembly
- Disassembly of Travel Motor
- Appearance of Motor
- Removal of counterbalance Valve
- Removal of Outer Piping
- Removal of Stroke Limiter
- Removal of Oil Seal
- Removal of Control Unit
- Removal of Control Valve
- Disassemble Control Valve
- Disassemble Stroke Limiter
- Reassemble Stroke Limiter
- Reassemble Control Valve
- Installation of Control Valve
- Reassembly of Travel Motor
- Assembly of Control Unit
- Installation of Oil Seal
- Installation of Stroke Limiter
- Installation of Outer Piping
- Installation of Counterbalance Valve
Main Pump S0708305
- General Description
- Composition
- Parts List
- Special Tools and Materials
- Special Tools
- Troubleshooting, Testing and Adjustment
- Disassembly
- General Disassembly
- Piston Pump Disassembly
- Control Parts Disassembly (Servo Case "AS")
- Cleaning and Inspection (Wear Limits and Tolerances)
- Piston Pump Inspection and Parts Substitution
- Reassembly
- Reassembly Piston Pump
- Reassembly Control Part
- Reassembly TVC Valve
- General Reassembly
- Shim Adjustment
Brake Supply Valve S0709220
- Parts List
- Specifications
Counterbalance Valve S0709300
- General Description
- While Operating to Run Forward
- While Operating to Stop
- While Operating to Back
- Adjustment of Relief Valve
- Troubleshooting
- Counterbalance Valve
- Recommended Tools
- Disassembly
- Order of Disassembly and Torque Values
- Reassembly
Main Control Valve (Toshiba DX28-60) S0709440
- Control Valve Operation
- Arm Priority Circuit
- Bucket (Junction) Circuit
- Main Relief Valve
- Overload Relief Valve
- Arm Load Holding Valve
- Boom Load Holding Valve
- Arm Regeneration
- Boom Regeneration
- Foot Relief Valve
- Parts List
- Specifications
- Control Valve Drawing and Hydraulic Circuit
- Disassembly and Reassembly
- General Disassembly
- General Reassembly
- Plunger Replacement
- Main Plunger Element - Disassembly and Assembly
- Tool
- Main Relief Valve
- Overload Relief Valve
- Arm Load Holding Valve
- Boom Load Holding Valve
- Arm Regeneration Valve
- Bucket Unity Check
- Foot Relief Valve
- Center Bypass Valve (CB Valve)
- Boom Parallel Switch Valve
- Boom Unity Check Valve
- Check Valve - Locations
- Check Valve
Pilot Control Valve (Work Lever / Joystick) S0709450
- General Description
- Theory of Operation
- Parts List
- Specifications
- Hydraulic Specifications
- Special Tools
- Disassembly
- Reassembly
Steering Valve S0709710
- General Description
- Theory of Operation
- Parts List
- Specifications
- Special Tools and Materials
- Special Tools
- Disassembly
- Reassembly
Dozer Control Valve S0709900
- Parts List
- Specifications
Hydraulic Schematic (Solar 170W-V) S0792140
- General Description
- Solar 170W-V with Standard Boom
- Solar 170W-V with Articulated Boom
- General Notes
ELECTRICAL SYSTEM
Electrical System S0802160
- Troubleshooting - Electrical System
- Wiring Harness Illustrations
- Overview
- Electric Supply System
- Engine Starting Circuit
- Operation During Start Process
- Operation After Start Process
- Engine Preheating System
- Engine Stop System
- Charging System
- Monitoring System
- Instrument Panel and Steering Console
- iNstrument Panel and Steering Console Function Check
- Monitoring System Schematic
- Operation
- Instruments
- Mode Select Switch
- Pilot Lights
- Initial Operation
- Electronic Hydraulic Control System (EPOS V)
- Power Mode Control
- Operation
- Throttle Position Sensor
- Power Mode Control - Circuit Diagram
- Work Mode Control
- Operation
- Work Mode Control - Circuit Diagram
- Engine Control System
- Engine Control Motor
- Engine Speed Control Dial
- Engine Control Circuit Diagram
- Automatic Deceleration Control (Auto Idle Control)
- Engine Overheat Protection System
- Power Boost Mode
- Operation
- Power Boost Control - Circuit Diagram
- Cruise Control
- Function
- Cruse Control Circuit
- Adjusting Method of Engine Control Unit
- Adjusting Method of Engine Control System
- Adjusting Method of Engine RPM
- Adjustment of TPS (Throttle Position Sensor)
- Self-diagnostic Function
- EPOS-V Controller
- Engine Throttle Controller
Electrical Schematic (Solar 170W-V) S0892140
- General Description
- Solar 170W-V
ATTACHMENTS
Boom and Arm S0902120
- Front Attachment Pin Specifications
- Front Attachment - Removal and Installation
- Arm Removal Procedure
- Boom Removal Procedure
- Installation
- Arm Installation Procedure
- Boom Installation Procedure
- Start-up Procedures
Bucket S0904000
- Bucket Tooth Inspection and Replacement
- Type 1
- Type 2
- Type 3
- Bucket O-ring Replacement
- Type 1
- Type 2
- Bucket Shimming Procedures
- New Bucket Installation
- Type 1
- Type 2
- Bucket Attachment, Removal and Reversal
- Detaching the Bucket
- Attaching The bucket
- Reversing the Bucket
S0792140.PDF
Hydraulic Schematic (Solar 170W-V) S0792140
- General Description
- Solar 170W-V with Standard Boom
- Solar 170W-V with Articulated Boom
- General Notes