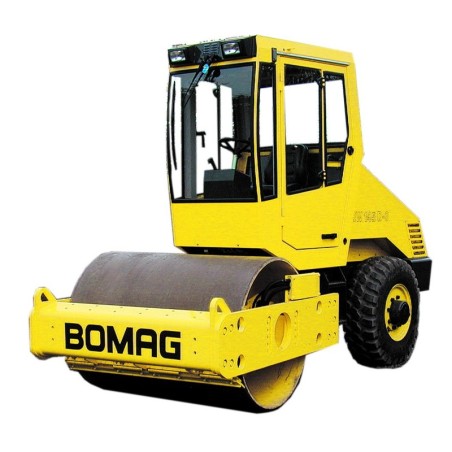
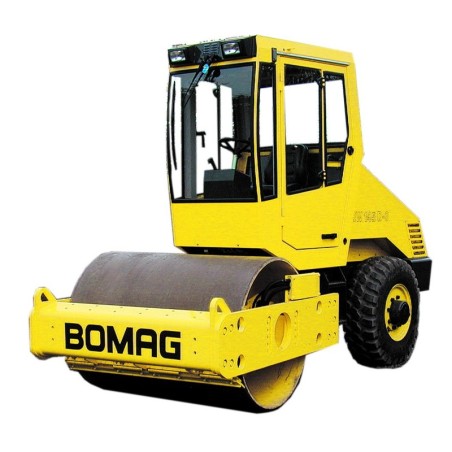
BOMAG BW145DH-3 - OPERATING MAINTENANCE MANUAL
- English Operating Maintenance Manual, to vehicles Bomag BW145DH-3.
CONTENTS:
BW 145 D-3 / DH-3 / PDH-3
- S/N 101 581 21.... 901 581 47 ....
- S/N 101 581 22.... 901 581 48 ....
- S/N 101 581 23 .... 901 581 49 ....
SINGLE DRUM ROLLER
- BOMAG machines are products from the wide range of BOMAG compaction equipment.
- BOMAG's vast experience, together with the most up-to-date production and testing methods, includ...
-- These instructions comprise:
-- Using these instructions will
-- Compliance with the maintenance instructions will
-- BOMAG shall not assume liability for safe functioning of the machine
-- No warranty claims can be lodged for damage resulting from
- Please note!
- For your own safety you should only use BOMAG-spare parts.
- We reserve the right for technical modifications without prior notification.
- Please fill in
-- Fig. 1
-- Fig. 2
-- Fig. 3
-- 1 Technical Data
-- Fig. 4
- BW 145 D-3
- BW 145 DH-3
- BW 145 PDH-3
- BW 145 D-3
- BW 145 DH-3
- BW 145 PDH-3
- Weights
- Travel characteristics
- Drive
- Brakes
- Steering
- Vibration
- Tires
- Tank contents
- The following noise and vibration values according to the EC-directive for machines, edition (91/...
- During operation these values may vary because of the existing operating conditions.
- Noise value
-- sound pressure level at the work place of the operator (with cabin):
-- sound capacity level:
- Vibration value
-- Vibration of the entire boy (driver’s seat)
-- Hand-arm vibration values
-- 2 Safety regulations
- General
-- This BOMAG machine is built in accordance with the latest technical standard and the valid techni...
-- Each person involved in operation, maintenance and repair of the machine must therefore read and ...
- Intended use
- Unintended use
- Who is allowed to work with the machine?
- Conversions and alterations to the machine
- Safety notes in the operating and maintenance instructions:
- Information and safety stickers/decals on the machine
- Loading the machine
- Towing the machine
- Checking the roll-over protection structure (ROPS)
- Starting the machine
-- Before starting
-- Starting
-- Starting with jump leads
-- Starting in closed rooms
- Driving the machine
-- Persons in the danger area
-- Driving
-- Driving on gradients and slopes
-- Behaviour in traffic
-- Check the effect of vibration
- Parking the machine
-- Parking on gradients or slopes
- Filling the fuel tank
-- Fire protection measures
- Maintenance work
-- Working on hydraulic lines
-- Changing of hydraulic hoses
-- Working on the engine
-- Working in the electric system
-- Working on the battery
-- Working on the fuel system
-- Working on wheels and tires
-- Cleaning
-- After maintenance work
- Repair
-- Test
-- 3 Indicators and Controls
-- Fig. 5
3.1 GENERAL NOTES
- Fig. 6
-- No. 1 = Multi-function display
- The control and warning lamps light up while the engine is running:
-- Fig. 7
-- No. 2 = Rotary switch for flashing beacon
-- Fig. 8
-- No. 3 = Rotary switch, lighting (StVZO)
-- Fig. 9
-- No. 4 = Rotary switch for hazard light system
-- Fig. 10
-- No. 5 = Rotary switch for direction indicators left / right
-- Fig. 11
-- No. 6 = Rotary switch working lights
-- Fig. 12
-- No. 7 = Rotary switch, vibration
-- Fig. 13
-- No. 8 = Rotary switch for speed range selection
-- Fig. 14
-- No. 9 = Push button for warning horn
-- Fig. 15
-- No. 10 = Emergency stop switch
-- Fig. 16
-- No. 11 = Ignition switch
-- Fig. 17
-- No. 12 = Push button for vibration
-- Fig. 18
-- No. 13 = Travel lever
-- Fig. 19
-- No. 14 = Throttle lever
-- No. 15 = Locking plate for throttle lever
-- Fig. 20
-- No. 16 = Fuses in electric installation box
-- Fig. 21
-- No. 17 = Main fuse for battery
-- Fig. 22
-- No. 18 = Pedal for dozer blade
-- Fig. 23
-- No. 19 = Fuse box, cabin
-- No. 20 = Toggle switch, heating blower
-- No. 21 = Toggle switch, flashing beacon
-- No. 22 = Toggle switch, windscreen wiper/ washer, front
-- No. 23 = Toggle switch, windscreen wiper/ washer, rear
-- No. 24 = Cabin light
-- No. 25 = Vent for fresh air intake
-- Fig. 24
-- No. 26 = Shut-off valve for cabin heater
-- 4 Operation
4.1 GENERAL NOTES
4.2 TESTS BEFORE TAKING INTO OPERATION
- Check:
4.3 STARTING THE ENGINE
- Fig. 25
- Fig. 26
- Fig. 27
- Fig. 28
- Fig. 29
- Fig. 30
- Fig. 31
- Fig. 32
- Fig. 33
4.4 STARTING WITH JUMP LEADS
- Fig. 34
4.5 DRIVING THE MACHINE
- Fig. 35
- Fig. 36
- Fig. 37
- Important notes on travel operation
4.6 EMERGENCY EXIT
4.7 OPERATING THE PARKING BRAKE, STOPPING THE MACHINE
- Fig. 38
4.8 SHUTTING THE ENGINE DOWN
- Fig. 39
- Fig. 40
- Fig. 41
4.9 SWITCHING THE VIBRATION ON AND OFF
- Preselecting the vibration
-- Fig. 42
- Switching the vibration on
-- Fig. 43
-- Fig. 44
- Switching the vibration off
4.10 ADJUSTING THE SEAT
- Fig. 45
4.11 OPERATING THE HOOD
- Fig. 46
- Fig. 47
4.12 TOWING IN CASE OF AN ENGINE FAILURE
- Fig. 48
- Fig. 49
- Fig. 50
- After towing
-- Fig. 51
-- Fig. 52
4.13 TRANSPORT
- Fig. 53
- Fig. 54
- Fig. 55
- Weights: See technical data
-- 5 Maintenance
5.1 GENERAL NOTES ON MAINTENANCE
- Notes on the fuel system
- Notes on the performance of the engine
- Notes on the hydraulic system
5.2 FUELS AND LUBRICANTS
- Engine oil
-- Quality
-- Approved engine oils
-- Oil viscosity
-- Fig. 56
-- Oil change intervals
-- ACEA
-- API
- Fuels
-- Quality
-- Winter fuel
-- Operation with rape seed oil methyl ester (RME „Bio Diesel“)
- Hydraulic oil
-- Bio-degradable hydraulic oil
- Oil for drive axle
- Lubrication grease
5.3 TABLE OF FUELS AND LUBRICANTS
- Assembly
- Fuel or lubricant
- Quantity approx.
- Summer
- Winter
5.4 RUNNING-IN INSTRUCTIONS
- The following maintenance work must be performed when running in new machines or overhauled engines:
- After 50 operating hours
- After 500 operating hours
5.5 MAINTENANCE CHART
- With all maintenance intervals perform also the work for shorter preceding service intervals.
- No.
- Designation
- Note
- Every 10 operating hours
- Every 250 operating hours
- Every 500 operating hours
- Every 1000 operating hours
- Every 2000 operating hours
- Every 3000 operating hours
- Every 5000 operating hours
- As required
5.6 CHECKING THE ENGINE OIL LEVEL
- Fig. 57
- For quality and quantity of oil refer to the table of fuels and lubricants
5.7 CHECKING THE FUEL FILTER WATER SEPARATOR
- Fig. 58
5.8 CHECKING THE FUEL LEVEL
- Fig. 59
- Fig. 60
- For quality of fuel refer to the table of fuels and lubricants.
5.9 CHECKING THE HYDRAULIC OIL LEVEL
- Fig. 61
- Normal level
- Minimum level
-- Fig. 62
- For quality and quantity of oil refer to the table of fuels and lubricants.
5.10 CHECKING THE TIRE PRESSURE
- Fig. 63
- Nominal value see "technical data".
5.11 CLEANING THE COOLING FINS ON THE RADIATOR
- Cleaning with compressed air
-- Fig. 64
- Cleaning with cold cleansing agent
5.12 CLEANING THE COOLING FINS ON THE HYDRAULIC OIL COOLER
- Cleaning with compressed air
-- Fig. 65
- Cleaning with cold cleansing agent
5.13 CHECK THE OIL LEVEL IN THE DRIVE AXLE
- Fig. 66
- For quality of oil refer to the table of fuels and lubricants.
5.14 CHECKING THE OIL LEVEL IN LEFT/ RIGHT WHEEL HUBS
- Fig. 67
- For quality of oil refer to the table of fuels and lubricants.
5.15 CHECKING THE OIL LEVEL IN THE VIBRATION BEARINGS
- Fig. 68
- For quality of oil refer to the table of fuels and lubricants.
5.16 SERVICING THE BATTERY
- Fig. 69
- Fig. 70
5.17 DRAINING THE SLUDGE FROM THE FUEL TANK
- Fig. 71
5.18 CHANGE ENGINE OIL AND OIL FILTER CARTRIDGE
- Fig. 72
- Fig. 73
- Fig. 74
- For quality and quantity of oil refer to the table of fuels and lubricants.
-- Fig. 75
-- Fig. 76
5.19 CHECKING THE V-BELT TENSION, TIGHTENING
- Checking the V-belt
-- Fig. 77
- Retightening the V-belt
-- Fig. 78
5.20 CHECKING, ADJUSTING THE VALVE CLEARANCE
- Valve clearance
-- Fig. 79
-- Fig. 80
-- Fig. 81
-- Fig. 82
- Adjusting the valve clearance
-- Fig. 83
5.21 CHANGING THE OIL IN THE VIBRATION BEARINGS
- Fig. 84
- Fig. 85
- For quality and quantity of oil refer to the table of fuels and lubricants.
5.22 CHANGE THE OIL IN THE DRIVE AXLE
- Fig. 86
- Fig. 87
- For quality and quantity of oil refer to the table of fuels and lubricants.
5.23 CHANGE THE OIL IN THE WHEEL HUBS
- Fig. 88
- Fig. 89
- For quality and quantity of oil refer to the table of fuels and lubricants.
5.24 CHANGING THE FUEL PRE-FILTER
- Fig. 90
5.25 CHANGING THE FUEL FILTER CARTRIDGE
- Fig. 91
5.26 CHECKING THE FASTENINGS ON THE DIESEL ENGINE
- Fig. 92
- Fig. 93
5.27 TIGHTENING THE FASTENING OF THE AXLE ON THE FRAME
- Fig. 94
5.28 TIGHTENING THE WHEEL NUTS
- Fig. 95
- Tightening torques 550 Nm (405 ft-lb) (M22x1,5)
5.29 CHECKING THE ROPS
- Fig. 96
5.30 CHANGING HYDRAULIC OIL AND BREATHER FILTER
- Fig. 97
- Fig. 98
- Nominal value:
- For quality and quantity of oil refer to the table of fuels and lubricants.
5.31 CHANGING THE HYDRAULIC OIL FILTER
- Fig. 99
5.32 CHECKING THE INJECTION VALVES
5.33 REPLACING THE TOOTHED BELT
- Fig. 100
5.34 CHECKING, CLEANING, CHANGING THE COMBUSTION AIR FILTER
- Fig. 101
- Fig. 102
- Fig. 103
- Fig. 104
- Fig. 105
- Fig. 106
- Fig. 107
- Dry cleaning of the main filter element
-- Fig. 108
- Changing the safety filter element
-- Fig. 109
5.35 ADJUSTING THE PARKING BRAKE
- Fig. 110
- Fig. 111
- Fig. 112
5.36 CHANGING THE TIRES
- Fig. 113
5.37 ADJUSTING THE SCRAPERS
- smooth drum only
-- Fig. 114
- padfoot drum only
-- Fig. 115
5.38 CHANGING THE FRESH AIR FILTER IN THE CABIN
- Fig. 116
5.39 TIGHTENING TORQUES
- Fig. 117
5.40 ENGINE CONSERVATION
- Anti-corrosion oils are those that comply with the specification MIL-L-21260 B or TL 9150- 037/2 ...
- A machine with a conserved engine must be marked by attaching a clearly visible warning tag.
-- 6 Trouble shooting
6.1 GENERAL NOTES
- The following work must only be carried out by qualified and trained personnel or by the sales se...
- Please observe strictly the safety regulations in chapter 2 of these operating and maintenance in...
6.2 ENGINE
- Faults
- Possible cause
- Remedy