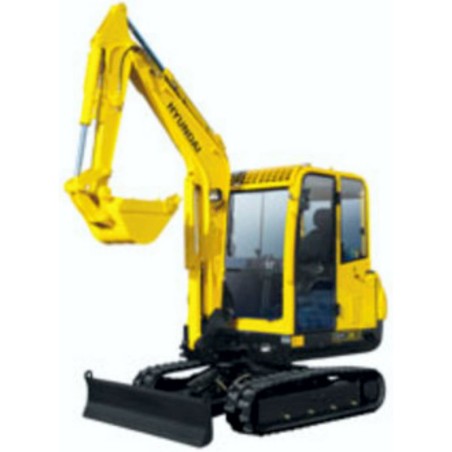
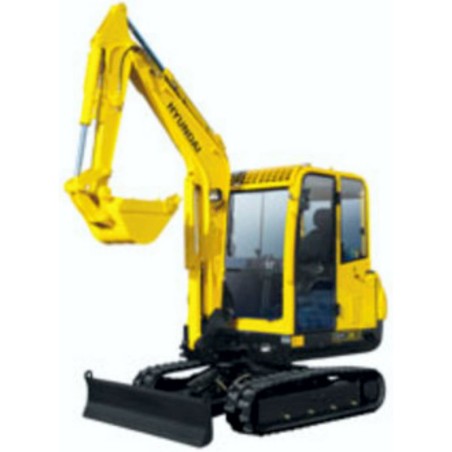
HYUNDAI R36N-7 - WORKSHOP, SERVICE, REPAIR MANUAL - OPERATORS MANUAL - WIRING DIAGRAMS
- English Service Manual, Operators Manual and Wiring Diagrams, for Mini Excavator Hyundai R36N-7.
CONTENTS:
SERVICE MANUAL
- Precautions on Maintenance
- Outline
- Attachment
- Engine
- Main Pump
- Hydraulic Oil Filter
- Control Valve
- Joystick
- Slew Motor
- Travel Motor
- Hydraulic Cylinder
- Swivel Joint
- Crawler
- Spring Case and Grease Cylinder
- Idler
- Sprocket
- Track Roller
- Electrical Equipment
- Troubleshooting
ENGINE SERVICE MANUAL
- INTRODUCTION
- HOW TO USE THIS MANUAL
- TABLE OF CONTENTS
- 1 MODEL IDENTIFICATION AND SERIAL NUMBER LOCATION
- 1.1 Model identification location
- 1.2 Serial Number Location
- 2 COMPONENT LOCATION
- 2.1 S3L/S3L2
- 2.2 Engine S3L-T/S3L2-T
- 2.3 S4L/S4L2
- 2.4 Engine S4L-T/S4L2-T
- 3 SPECIFICATIONS
- 4 DETERMINING WHEN TO OVERHAUL THE ENGINE
- 5 COMPRESSION PRESSURE MEASUREMENT
- 5.1 Inspection
- 5.2 Measurement
- 6 TROUBLESHOOTING
- 6.1 General
- 6.2 Engine troubleshooting
- 6.3 Starting system troubleshooting
- 7 BASIC PRECAUTIONS FOR DISASSEMBLY AND ASSEMBLY
- 7.1 Disassembly
- 7.2 Assembly
- 8 PREPARATION FOR DISASSEMBLY
- 8.1 Engine oil draining
- 8.2 Coolant draining 1
- 9 ELECTRICAL SYSTEM
- 9.1 Starter
- 9.2 Alternator
- 10 Cooling System
- 10.1 Cooling fan removal
- 10.2 Thermostat case removal
- 10.3 Water pump assembly removal
- 11 Fuel System
- 11.1 Fuel injection pipe removal
- 11.2 Fuel injection nozzle removal
- 11.3 Governor assembly removal
- 11.4 Governor weight removal
- 11.5 Fuel injection pump removal
- 12 Lubrication System
- 12.1 Oil filter removal
- 12.2 Pressure relief valve removal
- 12.3 Oil pressure switch removal
- 13 AIR INLET SYSTEM AND EXHAUST SYSTEM
- 13.1 Exhaust manifold removal
- 13.2 Air inlet cover removal
- 14 CYLINDER HEAD AND VALVE MECHANISM
- 14.1 Rocker shaft assembly removal
- 14.2 Rocker shaft disassembly
- 14.3 Cylinder head bolt removal
- 14.4 Cylinder head assembly removal
- 14.5 Valve and valve spring removal
- 14.6 Valve stem seal removal
- 15 Timing Gears and Flywheel
- 15.1 Flywheel removal
- 15.2 Rear plate removal
- 15.3 Oil seal case removal
- 15.4 Tappet removal
- 15.5 Speedometer driven gear removal
- 15.6 Crankshaft pulley removal
- 15.7 Timing gear case removal
- 15.8 Timing gear backlash measurement
- 15.9 Idler gear removal
- 15.10 Camshaft removal
- 15.11 Fuel injection pump camshaft removal
- 15.12 Gear removal (when required)
- 15.13 Oil pump removal
- 15.14 Front plate removal
- 16 Cylinder Block, Crankshaft, Pistons and Oil Pan
- 16.1 Oil pan removal
- 16.2 Oil screen removal
- 16.3 Thrust clearance measurement for connecting rod big end
- 16.4 Connecting rod cap removal
- 16.5 Piston removal
- 16.6 End play measurement for crankshaft
- 16.7 Main bearing cap removal
- 16.8 Crankshaft removal
- 16.9 Piston separation from connecting rod
- 17 CYLINDER HEAD AND VALVE MECHANISM
- 17.1 Cylinder head
- 17.2 Rocker arms and rocker shaft
- 17.3 Valve springs
- 17.4 Valve push rods
- 17.5 Valves, valve guides and valve seats
- 17.6 Combustion jet replacement
- 18 TIMING GEARS AND FLYWHEEL
- 18.1 Camshaft
- 18.2 Fuel injection pump camshaft
- 18.3 Tappets
- 18.4 Idler gear
- 18.5 Flywheel and ring gear
- 19 CYLINDER BLOCK, CRANKSHAFT, PISTONS AND OIL PAN
- 19.1 Pistons, Piston Rings and Piston Pins
- 19.2 Connecting rods
- 19.3 Crankshaft
- 19.4 Cylinder block
- 20 Cylinder Block, Crankshaft, Pistons and Oil pan
- 20.1 Main bearing installation
- 20.2 Crankshaft installation
- 20.3 Main bearing cap installation
- 20.4 Side seal installation
- 20.5 Piston assembling to connecting rod
- 20.6 Piston ring installation
- 20.7 Piston and connecting rod installation
- 20.8 Connecting rod cap installation
- 20.9 Oil screen installation
- 20.10 Oil pan installation
- 21 Timing Gears and Flywheel
- 21.1 Front plate installation
- 21.2 Oil pump installation
- 21.3 Engine turning
- 21.4 Engine turning
- 21.5 Camshaft installation
- 21.6 Idler gear installation
- 21.7 Timing gear case installation
- 21.8 Crankshaft pulley nut tightening
- 21.9 P.T.O. gear installation
- 21.10 Speedometer driven gear installation
- 21.11 Tappet installation
- 21.12 Oil seal case installation
- 21.13 Rear plate installation
- 21.14 Flywheel installation
- 22 CYLINDER HEAD AND VALVE MECHANISM
- 22.1 Cylinder head bottom face cleaning
- 22.2 Valve stem seal installation
- 22.3 Valve spring installation
- 22.4 Installing valve block
- 22.5 Cylinder head gasket installation
- 22.6 Cylinder head installation
- 22.7 Cylinder head bolt tightening
- 22.8 Valve push rod installation
- 22.9 Rocker shaft assembling
- 22.10 Rocker shaft assembly installation
- 22.11 Valve clearance adjustment
- 22.12 Rocker cover installation
- 23 Air Inlet System and Exhaust System
- 23.1 Air inlet cover installation
- 23.2 Exhaust manifold installation
- 24 Fuel System
- 24.1 Fuel injection nozzle installation
- 24.2 Fuel injection pump installation
- 24.3 Flyweight assembly installation
- 24.4 Sliding sleeve installation
- 24.5 Governor assembly installation
- 24.6 Fuel injection line installation
- 25 Lubrication system
- 25.1 Pressure relief valve installation
- 25.2 Oil filter installation
- 25.3 Oil pressure switch installation
- 26 Cooling system
- 26.1 Water pump installation
- 26.2 Thermostat installation
- 26.3 Cooling fan installation
- 26.4 Thermoswitch and thermounit combination installation
- 27 Electrical System
- 27.1 Glow plug installation
- 27.2 Alternator installation
- 28 GENERAL
- 28.1 Specifications (standard)
- 28.2 Wiring diagrams
- 29 STARTER
- 29.1 Disassembly
- 29.2 Inspection
- 29.3 Assembly
- 29.4 Inspection and Testing after Assembly
- 30 ALTERNATOR
- 30.1 Disassembly
- 30.2 Inspection
- 30.3 Assembly
- 31 KEY SHUTOFF SYSTEM (ETS solenoid type)
- 31.1 General
- 31.2 Cord color (standard)
- 31.3 Shutoff solenoid installation
- 31.4 Inspection after assembly
- 32 KEY SHUTOFF SYSTEM (ETR solenoid type)
- 32.1 General
- 32.2 Cord color (standard)
- 32.3 Shutoff solenoid installation
- 33 AUTOMATIC GLOW SYSTEM
- 33.1 General
- 33.2 Glow timer specification (standard)
- 33.3 Glow plug relay specifications (standard)
- 33.4 Glow plug inspection
- 34 GENERAL
- 34.1 Schematic
- 34.2 Specifications (standard)
- 35 INSPECTION
- 35.1 Water pump
- 35.2 Thermostat (standard)
- 35.3 Thermoswitch (standard)
- 35.4 Thermounit (standard)
- 36 GENERAL
- 36.1 Schematic
- 36.2 Specifications
- 37 INSPECTION
- 37.1 Oil pump
- 37.2 Oil pressure switch
- 37.3 Pressure relief valve
- 38 GENERAL
- 38.1 Schematic
- 38.2 Specifications (standard)
- 39 FUEL INJECTION NOZZLE
- 39.1 Inspection
- 39.2 Disassembly and assembly
- 40 FUEL INJECTION PUMP
- 40.1 Test on engine
- 40.2 Disassembly
- 40.3 Inspection
- 40.4 Assembly
- 41 GOVERNOR
- 41.1 Disassembly and inspection
- 41.2 Assembly
- 41.3 Torque spring set installation
- 42 FUEL PUMP
- 42.1 Inspection
- 43 FUEL FILTER
- 44 GENERAL
- 44.1 Schematic
- 45 INSPECTION
- 45.1 Inspection procedure
- 46 LUBRICATION AND MAINTENANCE CHART
- 47 ENGINE OIL AND OIL FILTER
- 47.1 Engine oil specifications
- 47.2 Oil level check
- 47.3 Oil and oil filter change
- 47.4 Oil filter change
- 48 VALVE CLEARANCE
- 49 FUEL INJECTION TIMING
- 49.1 Preparation
- 49.3 Adjustment
- 50 FUEL FILTER
- 50.1 Fuel filter with [AIR] valve
- 50.2 Cartridge (air vent screw) type fuel filter
- 51 FUEL SYSTEM PRIMING
- 51.1 Engine with fuel filter with [AIR] valve
- 51.2 Engine with cartridge (air vent screw) type fuel filter
- 52 IDLE RPM SETTING
- 53 FUEL INJECTION NOZZLES
- 53.1 Injection pressure (valve opening pressure) test
- 53.2 Orifice restriction test
- 53.3 Nozzle tip washing and replacement
- 53.4 Installation
- 54 FAN BELT
- 55 SPECIFICATIONS
- 55.1 Basic engine components
- 55.2 Lubrication system
- 55.3 Fuel system
- 55.4 Air inlet system and exhaust system
- 55.5 Cooling system (standard)
- 55.6 Electrical system
- 56 TIGHTENING TORQUES
- 56.1 Major bolts and nuts
- 56.2 Torques for bolts and nuts with standard threads
- 56.3 Torques for plugs with taperlock threads
- 57 SEALANTS
- 58 SPECIAL TOOLS
OPERATORS MANUAL
- OPERATION
- Safety Decals 1
- Basic Precautoins on Safety 3
- Safety Precautionary Notes before Start 4
- Safety Precautions during Operation 6
- Safety Precautions during Inspection and Maintenance 15
- Safety Post Operational Caution 18
- Part Names 19
- Explanation of Each Device 21
- Operation 28
- Operational Precautions 32
- Transporting by Truck 39
- Machine Traction 41
- How to Hoist a Machine 42
- Cold Weather or During-Winter Operations 44
- Long-Period Storage 46
- INSPECTION AND MAINTENANCE
- Ordering Parts and Servicing Guidelines 47
- Inspections 48
- Maintenance after the First 50 Service Hours (New Machine) 53
- Maintenance after the First 100 Service Hours (New Machine) 54
- Maintenance Every 50 Service Hours 55
- Maintenance Every 100 Service Hours 57
- Maintenance Every 250 Service Hours 58
- Maintenance Every 500 Service Hours 59
- Maintenance Every 1000 Service Hours 61
- To Pressurize 62
- Inspection and Maintenance Procedures for Engine Parts 64
- Inspection and Maintenance Procedures 65
- Periodical Inspections and Maintenance List 69
- Lubricants 71
- OTHERS
- Dimensions and Specifications 75
- Hydraulic Circuit 77
- Electric Circuit 78