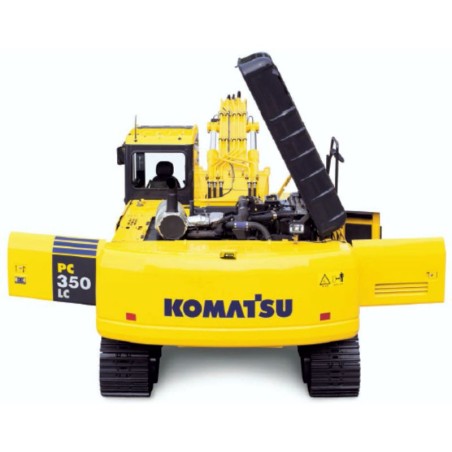
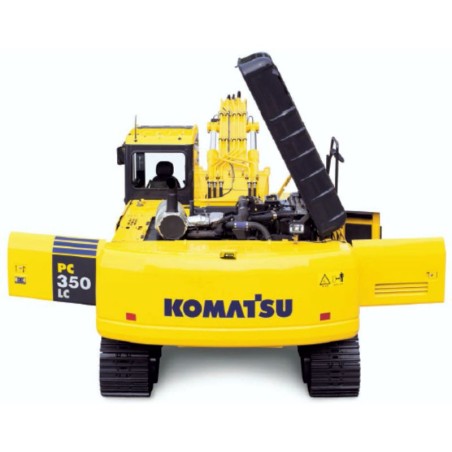
KOMATSU PC350LC-8, PC350LCD-8, PC350NLC-8, PC350NLCD-8 - WORKSHOP, SERVICE, REPAIR MANUAL - WIRING DIAGRAMS
- English Service Manual and Wiring Diagrams, for Komatsu PC350LC-8, PC350LCD-8, PC350NLC-8, PC350NLCD-8.
CONTENTS:
- CONTENTS
- REVISED PAGES
- SAFETY
- Safety Notice
- GENERAL
- HOW TO READ THE SHOP MANUAL
- Volumes
- Distribution and Updating
- Filing Method
- Revised Edition Mark
- Revisions
- Symbols
- HOISTING INSTRUCTIONS
- Hoisting
- Wire Ropes
- PUSH PULL COUPLER
- Type 1
- Type 2
- Type 3
- COATING MATERIALS
- STANDARD TIGHTENING TORQUE
- Standard Tightening Torque of Bolts And Nuts
- Tightening Torque of Hose Nuts
- Tightening Torque of Split Flange Bolts
- Tightening Torque for Flared Nuts
- Table of Tightening Torques for O-ring Boss Piping Joints
- Table of Tightening Torques for O-ring Boss Plugs
- Tightening Torque Table for Hoses (Taper Seal Type and Face Seal Type)
- ELECTRIC WIRE CODE
- Classification by Thickness
- Classification by Color and Code
- CONVERSION TABLES
- Method of Using the Conversion Table
01 GENERAL
- SPECIFICATION DIMENSION DRAWINGS
- Dimensions
- Working Ranges
- SPECIFICATIONS
- WEIGHT TABLE
- FUEL, COOLANT, AND LUBRICANTS
10 STRUCTURE, FUNCTION ANDMAINTENANCE STANDARD
- ENGINE AND COOLING SYSTEM
- Engine Related Parts
- Radiator, Oil Cooler and Aftercooler
- POWER TRAIN
- Power Train
- Final Drive
- Sprocket
- Swing Machinery
- Swing Circle
- UNDERCARRIAGE AND FRAME
- Track Frame and Recoil Spring
- Idler
- Carrier Roller
- Track Roller
- Track Shoe
- Triple Grouser Shoe
- HYDRAULIC SYSTEM
- Hydraulic Equipment Layout Drawing
- Hydraulic Tank and Filter
- Hydraulic Pump
- Control Valve
- CLSS (Closed Center Load Sensing System)
- Valve Functions and Operation
- Valve Control
- Hydraulic Cylinder
- WORK EQUIPMENT
- Work Equipment
- AIR CONDITIONER PIPING
- ELECTRICAL SYSTEM
- Engine Control
- Sensors
- ELECTRONIC CONTROL SYSTEM
- Control Function
- System Diagram
- Engine and Pump Control
- Pump and Valve Control
- Power Maximizing and Machine Push-up
- Auto-deceleration
- Auto-warm-up and Overheat Prevention
- Swing Control
- Travel Control
- Attachment Flow Control and Circuit Selector
- System Component Parts
- MONITOR SYSTEM
- Machine Monitor
- KOMTRAX Terminal System
- KOMTRAX Communication Modem - TH300
20 STANDARD VALUE TABLES
- STANDARD VALUE TABLES
- Engine Related
- Chassis Related
30 TESTING AND ADJUSTING
- CHASSIS SERVICE TOOLS
- Sketches of special tools
- ENGINE
- Engine Speed
- Air Boost Pressure
- Exhaust Gas Color
- Valve Clearance
- Compression Pressure
- Blow-by Pressure
- Engine Oil Pressure
- Fuel Pressure
- Handling During Cylinder Cut-out Operation
- Handling During No Injection Cranking Operation
- Fuel Return Rate And Leakage
- Bleeding Air From Fuel Circuit
- Fuel Circuit For Leakage
- AIR COMPRESSOR BELT TENSION
- FAN BELT
- ALTERNATOR BELT
- SWING CIRCLE BEARINGS
- TRACK SHOE TENSION
- OIL PRESSURE IN WORK EQUIPMENT
- OIL PRESSURE IN SWING
- OIL PRESSURE IN TRAVEL CIRCUIT
- CONTROL CIRCUIT OIL PRESSURE
- PUMP PC OIL PRESSURE
- PUMP LS OIL PRESSURE
- SOLENOID VALVE OUTPUT PRESSURE
- PPC VALVE OUTPUT PRESSURE
- WORK EQUIPMENT VALVE ADJUSTMENT
- SWING PPC VALVE ADJUSTMENT
- HYDRAULIC DRIFT IN WORK EQUIPMENT
- Boom and Bucket Cylinders
- Arm Cylinder
- Boom Lock Valve
- PPC Valve
- RELEASING HYDRAULIC PRESSURE
- Oil Leakage Amount
- BLEEDING AIR FROM VARIOUS SYSTEMS
- DIODE INSPECTION PROCEDURES
- MACHINE MONITOR - SPECIAL FUNCTIONS
- Ordinary Functions and Special Functions of Machine Monitor
- Operator Mode (Outline)
- Service Mode
- Long Distance Transport Mode
- HANDLING VOLTAGE CIRCUIT OF ENGINE CONTROLLER
- PREPARATION WORK FOR TROUBLESHOOTING OF ELECTRICAL SYSTEM
- PROCEDURE FOR TESTING DIODES
- PM CLINIC SERVICE
40 TROUBLESHOOTING
- FAILURE CODES TABLE
- FUSE LOCATIONS
- Connection Table of Fuse Box
- Locations of Fusible Links
- Location of Fuse Box and Fuse Numbers
- GENERAL INFORMATION
- Points to Remember when Troubleshooting
- Sequence of Events in Troubleshooting
- Handling Electric Equipment and Hydraulic Components
- Connectors for Tier 3 Engines
- Checks Before Troubleshooting
- Classification and Troubleshooting Steps
- Connection Table for Connector Pin Numbers
- T-adapter Box and T-adapter Table
- FAILURE CODE (DISPLAY OF CODE)
- 989L00 - Engine Controller Lock Caution 1
- 989L00 - Engine Controller Lock Caution 2
- 989L00 - Engine Controller Lock Caution 3
- AA10NX - Air Cleaner Clogging
- AB00KE - Charge Voltage Low
- B@BAZG - Engine Oil Pressure Low
- B@BAZK - Engine Oil Level Low
- B@BCNS - Engine Coolant Overheat
- B@BCZK - Engine Coolant Level Low
- B@HANS - Hydraulic Oil Overheat
- CA111 - EMC Critical Internal Failure
- CA115 - Engine NE and BKUP Speed Sensor Error
- CA122 - Charge Air Pressure Sensor High Error
- CA123 - Charge Air Pressure Sensor Low Error
- CA131 - Throttle Sensor High Error
- CA132 - Throttle Sensor Low Error
- CA144 - Coolant Temperature Sensor High Error
- CA145 - Coolant Temperature Sensor Low Error
- CA153 - Charge Air Temperature Sensor High Error
- CA154 - Charge Air Temperature Sensor Low Error
- CA155 - Chg Air Temp High Speed Derate
- CA187 - Sensor Power Supply Two Volt Low Error
- CA221 - Ambient Pressure Sensor High Error
- CA222 - Ambient Pressure Sensor Low Error
- CA227 - Sensor Supply Two Volt High Error
- CA234 - Engine Overspeed
- CA238 - NE Speed Sensor Supply Voltage Error
- CA271 - IMV/PCV1 Short Error
- CA272 - IMV/PCV1 Open Error
- CA281 - Pump Press Balance Error
- CA322 - Injector #1 Open/short Error
- CA323 - Injector #5 Open/short Error
- CA324 - Injector #3 Open/short Error
- CA325 - Injector #6 Open/short Error
- CA331 - Injector #2 Open/short Error
- CA332 - Injector #4 Open/short Error
- CA342 - Calibration Code Incompatibility
- CA351 - Injectors Drive Circuit Error
- CA352 - Sensor Supply One Volt Low Error
- CA386 - Sensor Supply One Volt High Error
- CA428 - Water in Fuel Sensor High Error
- CA429 - Water in Fuel Sensor Low Error
- CA435 - Eng Oil Press Sw Error
- CA441 - Battery Voltage Low Error
- CA442 - Battery Voltage High Error
- CA449 - Rail Pressure Very High Error
- CA451 - Rail Pressure Sensor High Error
- CA452 - Rail Pressure Sensor Low Error
- CA488 - Chg Air Temp High Torque Derate
- CA553 - Rail Pressure High Error
- CA559 - Rail Pressure Low Error
- CA689 - Engine NE Speed Sensor Error
- CA731 - Engine BKUP Speed Sensor Phase Error
- CA757 - All Persistent Data Lost Error
- CA778 - Engine BKUP Speed Sensor Error
- CA1633 - KOMNET Datalink Timeout Error
- CA2185 - Throttle Sensor Supply Volt High Error
- CA2186 - Throttle Sensor Supply Volt Low Error
- CA2249 - Rail Pressure Very Low Error
- CA2265 - Electric Lift Pump High Error
- CA2266 - Electric Lift Pump Low Error
- CA2311 - IMV Solenoid Error
- CA2555 - Grid Htr Relay Volt High Error
- CA2556 - Grid Htr Relay Volt Low Error
- D110KB - Battery Relay Drive S/C
- D19JKZ - Personal Code Relay Abnormality
- D862KA - GPS Antenna Discon
- DA22KK - Pump Solenoid Power Low Error
- DA25KP - 5 V Sensor 1 Power Abnormality
- DA29KQ - Model Selection Abnormality
- DA2RMC - Pump Communication Abnormality
- DAF8KB - Short Circuit in Camera Power Supply
- DAFGMC - GPS Module Error
- DAFRMC - CAN Discon (Monitor Detected)
- DGH2KB - Hyd Oil Sensor Short
- DHPAMA - F Pump Pressure Sensor Abnormality
- DHPBMA - R Pump Pressure Sensor Abnormality
- DHS3MA - Arm Curl PPC Sensor Abnormality
- DHS4MA - Bucket Curl PPC Pressure Sensor Abnormality
- DHX1MA - Overload Sensor Abnormality (Analog)
- DW43KA - Travel Speed Solenoid Disconnection
- DW43KB - Travel Speed Solenoid S/C
- DW45KA - Swing Brake Solenoid Disconnection
- DW45KB - Swing Brake Solenoid S/C
- DW91KA - Travel Junction Solenoid Disconnection
- DW91KB - Travel Junction Solenoid S/C
- DWA2KA - Attachment Sol Open Circuit
- DWA2KB - Attachment Sol Short Circuit
- DWJ0KA - Merge-Divider Solenoid Disconnection
- DWJ0KB - Merge-Divider Solenoid S/C
- DWK0KA - 2-Stage Relief Sol. Open Circuit
- DWK0KB - 2-Stage Relief Solenoid Short Circuit
- DXA0KA - PC-EPC Solenoid Open Circuit
- DXA0KB - PC-EPC Solenoid Short Circuit
- DXE0KA - LS-EPC Solenoid Disconnection
- DXE0KB - LS-EPC Solenoid Short Circuit
- DXE4KA - Service Current EPC Disconnection
- DXE4KB - Service Current EPC Short Circuit
- DY20KA - Wiper Working Abnormality
- DY20MA - Wiper Parking Abnormality
- DY2CKA - Washer Drive Open Circuit
- DY2CKB - Washer Drive Short Circuit
- DY2DKB - Wiper Motor Drive Forward System Short
- DY2EKB - Wiper Drive Reverse Short Circuit
- E-MODE (ELECTRICAL SYSTEM)
- Information Contained in Troubleshooting Table
- E-1 Engine Does Not Start
- E-2 Auto-decelerator Does Not Operate
- E-3 Automatic Warming-up System Does Not Operate
- E-4 Preheater Does Not Operate
- E-5 All Work Equipment, Swing, and Travel Mechanism do not move
- E-6 Power Maximizing Function Does Not Operate
- E-7 Machine Monitor Does Not Display At All
- E-8 Machine Monitor Does Not Display Some Items
- E-9 Contents of Display by Machine Monitor are Different from Applicable Machine
- E-10 Fuel Level Monitor Was Lit in Red While Engine Running
- E-11 Engine Coolant Temperature Gauge Does Not Indicate Normally
- E-12 Hydraulic Oil Temperature Gauge Does Not Indicate Normally
- E-13 Fuel Level Gauge Does Not Indicate Normally
- E-14 Swing Lock Monitor Does Not Indicate Normally
- E-15 When Monitor Switch is Operated, Monitor Displays Nothing
- E-16 Windshield Wiper and Window Washer do not Operate
- E-17 Machine Push-up Function Does Not Operate Normally
- E-18 Monitoring Function Fails to Display “Boom Raise” Normally
- E-19 Monitoring Function Fails to Display “Boom Lower” Normally
- E-20 Monitoring Function Fails to Display “Arm In” Normally
- E-21 Monitoring Function Fails to Display “Arm Out” Normally
- E-22 Monitoring Function Fails to Display “Bucket Curl” Normally
- E-23 Monitoring Function Fails to Display “Bucket Dump” Normally
- E-24 Monitoring Function Fails to Display “Swing” Normally
- E-25 Monitoring Function Fails to Display “Travel” Normally
- E-26 Monitoring Function Fails to Display “Travel Differential Pressure” Normally
- E-27 Monitoring Function Fails to Display “Service” Normally
- E-28 KOMTRAX System Does Not Operate Normally
- E-29 Air Conditioner Does Not Operate
- E-30 Travel Alarm Does Not Sound or Does Not Stop Sounding
- E-31 Horn Does Not Sound
- H-MODE (HYDRAULIC AND MECHANICAL SYSTEMS)
- System Chart for Hydraulic and Mechanical System
- Information Contained in Troubleshooting Table
- H-1 All Work Equipment Lack Power, or Travel and Swing Speeds are Slow
- H-2 Engine Speed Sharply Drops or Engine Stalls
- H-3 No Work Equipment, Swing or Travel Move
- H-4 Abnormal Noise is Heard from Around Hydraulic Pump
- H-5 Auto-decelerator Does Not Work
- H-6 Fine Control Mode Does Not Function or Responds Slow
- H-7 Boom Moves Slowly or Lacks Power
- H-8 Arm Moves Slowly or Lacks Power
- H-9 Bucket Moves Slowly or Lacks Power
- H-10 Work Equipment Does Not Move in its Single Operation
- H-11 Work Equipment has a bit too Fast Hydraulic Drift
- H-12 Work Equipment Has Big Time Lag
- H-13 Other Work Equipment Moves When Relieving Single Circuit
- H-14 Power Max. Switch Does Not Operate
- H-15 In Compound Operation, Work Equipment with Larger Load Moves Slowly
- H-16 In Swing + Boom Raise Operation, Boom Moves Slowly
- H-17 In Swing + Travel Operation, Travel Speed Drops Sharply
- H-18 Machine Swerves in Travel
- H-19 Machine Travels Slowly
- H-20 Machine Cannot Be Easily Steered or Lacks Power
- H-21 Travel Speed Does Not Shift, or it is too Slow or Fast
- H-22 Track Shoe Does Not Turn (On One Side Only)
- H-23 Machine Does Not Swing
- H-24 Swing Acceleration is Poor, or Swing Speed is Slow
- H-25 Excessive Overrun When Stopping Swing
- H-26 There is Big Shock when Stopping Swing
- H-27 Large Sound is made when Upper Structure Stops Swinging
- H-28 Swing Hydraulic Drift is too big
50 DISASSEMBLY AND ASSEMBLY
- HOW TO READ THIS MANUAL
- SPECIAL TOOLS LIST
- SKETCHES OF SPECIAL TOOLS
- CONNECTOR REPAIR PROCEDURES
- Contact Terminal Removal (HD30 Type)
- Striping Insulation
- Crimping Contact Terminal (HD30 Type)
- Insertion Of Contact Terminal (HD30 Type)
- Contact Terminal Removal (DT Type)
- ENGINE COMPONENTS
- Fuel Supply Pump
- Engine Front Seal
- Removal
- Engine Rear Seal
- Cylinder Head
- RADIATOR
- Removal
- Installation
- HYDRAULIC OIL COOLER
- Removal
- Installation
- AFTERCOOLER
- Removal
- Installation
- ENGINE AND HYDRAULIC PUMP
- Removal
- Installation
- FINAL DRIVE
- Removal
- Installation
- Disassembly
- Assembly
- SWING MOTOR AND SWING MACHINERY
- Removal
- Installation
- Disassembly
- Assembly
- SWING CIRCLE
- Removal
- Installation
- CARRIER ROLLER
- Disassembly
- Assembly
- TRACK ROLLER
- Disassembly
- Assembly
- IDLER
- Disassembly
- Assembly
- RECOIL SPRING
- Disassembly
- Assembly
- SPROCKET
- Removal
- Installation
- TRACK SHOE
- Expansion
- Installation
- REVOLVING FRAME
- Removal
- Installation
- COUNTERWEIGHT
- Removal
- Installation
- CENTER SWIVEL JOINT
- Removal
- Installation
- Disassembly
- Assembly
- HYDRAULIC TANK
- Removal
- Installation
- CONTROL VALVE
- Removal
- Installation
- Disassembly
- Assembly
- HYDRAULIC PUMP
- Removal
- Installation
- Oil Seal in Hydraulic Pump input Shaft
- WORK EQUIPMENT PPC VALVE
- Disassembly
- Assembly
- TRAVEL PPC VALVE
- Disassembly
- Assembly
- HYDRAULIC CYLINDER
- Disassembly
- Assembly
- WORK EQUIPMENT
- Removal
- Installation
- CAB
- Removal
- Installation
- Cab Glass (Stuck Glass)
- Front Window
- Floor Frame
- ELECTRICAL SYSTEM
- Air Conditioner Unit
- KOMTRAX Communication Modem
- Monitor
- Pump Controller
- Engine Controller
60 AIR CONDITIONER
- STRUCTURE AND FUNCTION
- Air Conditioner Component
- Configuration and Function of Refrigerating cycle
- Outline of Refrigerating Cycle
- Air Conditioner Unit
- Functions of Major Components in the Air Conditioner Unit
- Control Plate
- Compressor
- Condenser and Receiver Drier
- TESTING AND ADJUSTING
- Caution About Refrigerant
- Troubleshooting Procedure
- Block Diagram
- Circuit Diagram and Arrangement of Connector Pins
- Detail of Air Conditioner Unit
- Part and Connector Locations
- Testing Air Leakage (Ducts)
- Testing with Self-diagnosis Function
- Testing Temperature Control
- Testing Vent (Mode) Changeover
- Testing Recirc/Fresh Changeover
- Testing Inner Sensor
- Testing Evaporator Temperature Sensor
- Testing Sunlight Sensor
- Testing (Dual) Pressure Switch for Refrigerant
- Testing Relays
- TROUBLESHOOTING
- Troubleshooting Chart 1
- Troubleshooting Chart 2
- Troubleshooting for Electrical System (E mode)
- Troubleshooting With Gauge Pressure
- Connection of Service Tool
- Precautions for connecting air conditioner piping
- Handling of Compressor Oil
- Desiccant Replacement Procedure
90 DIAGRAMS AND DRAWINGS
- HYDRAULIC DIAGRAM
- ELECTRICAL SYSTEM
- Electrical Circuit Diagram (1/5)
- Electrical Circuit Diagram (2/5)
- Electrical Circuit Diagram (3/5)
- Electrical Circuit Diagram (4/5)
- Electrical Circuit Diagram (5/5)