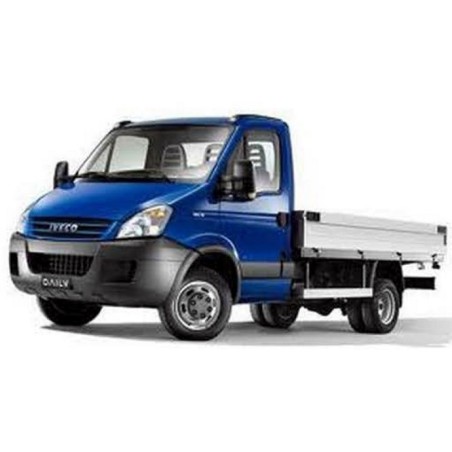
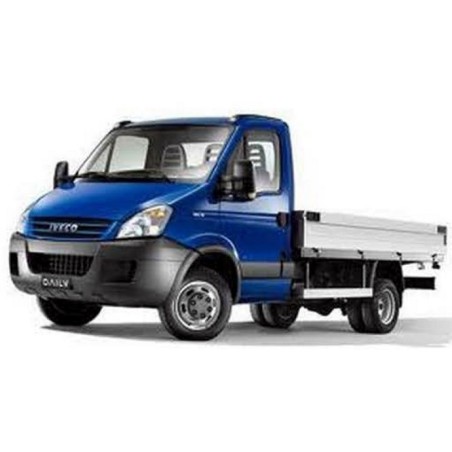
IVECO DAILY (2004) - WORKSHOP, SERVICE, REPAIR MANUAL - WIRING DIAGRAMS
- English Service Manual and Wiring Diagrams, to vehicles Iveco Daily (2004).
CONTENTS:
SECTION 1 - GENERAL
General
- Identification data
- Vehicle identification plate
- Composition of models
- Alphanumerical coding for vehicle identification
- Replenishing fluids
SECTION 2 - ENGINE
Engine
- F1a engine
- Main operations on engine mounted on vehicle
- Power unit removal/refitting
- Replacing belts
- Replacing the electric injectors
- Cylinder head removal and refitting
- Replacing high-pressure pump cph1
- Experimental tools
- Tightening torque
- Overhauling engine
- Disassembling the engineat the bench
- Repairs
- Cylinder block
- Crankshaft
- Engine assembly
- Engine flywheel
- Connecting rod - piston assembly
- Cylinder heads
- Valves
- Valve guide
- Valve seats
- Valve springs
- Rocker arms - tappets
- Rocker arms - tappets
- Assembling cylinder heads
- Timing system
- Lubrication
- Oil vacuum pump assembly (gpod)
- Cooling
- Turbocharging
- Repairs
- Repairs
- Exhaust gas recirculation (egr) system (exhaust gas recirculation)
- Exhaust pollutant reduction system with dpf catalyst (on request)
- D.p.f. (diesel particulate filter) catalyst
- Particulate filter regeneration system
- Fuel supply
- High-pressure electronic injection system (ms 6.3 - edc 16)
- System operation
- Operation
- Hydraulic system
- Electro-injectors
- Electric/electronic components
- Sensors
- Actuators
- F1c engine
- Main operations on engine mounted on vehicle
- Power unit removal/refitting
- Checks and tests
- Replacing air-conditioning compressor drive belt
- Power steering pump-alternator belt replacement
- Replacing the water pump
- Replacing the high-pressure pump
- Replacing the power steering pump
- Replacing the drive shaft seal ring and the front cover gasket
- Replacing the vacuum pumpoil pump assembly (gpod)
- Replacing the drive shaft rear seal ring
- Replacing electro-injectors
- Removal/refitting the cylinder head
- Egr heat exchanger removal - refitting
- Egr heat exchanger removal-refitting
- Burnt gas exhaust system
- Removal/refitting of exhaust pipe assembly components (systems equipped with d.p.f. Catalyst)
- Engine views
- Emissions
- Engine identification code
- Characteristic curves
- General specifications
- Assembly data - clearances
- Tools
- Experimental tools
- Tightening torque
- Overhauling engine f1c
- Disassembling the engineat the bench
- Repairs
- Cylinder block
- Crankshaft
- Engine assembly
- Engine flywheel
- Connecting rod - piston assembly
- Cylinder heads
- Valves
- Valve guide
- Valve seats
- Valve springs
- Rocker arms - tappets
- Assembling cylinder heads
- Timing system
- Auxiliary organ controls
- Timing system control
- Lubrication
- Oil pump/depressor unit
- Cooling
- Turbocharging
- Repairs
- Repairs
- Exhaust gas recirculation (egr) system
- Exhaust system removal-refitting
- System to reduce pollutants at exhaust
- Fuel supply
- High-pressure electronic injection system (edc 16)
- System operation
- Operation
- Hydraulic system
- Feed system and fuel recirculation
- Hydraulic system
- Electro-injectors
- Electric/electronic components
- Sensors
- Actuators
SECTION 3 - CLUTCH
Clutch
- Description
- Diagnostics
- Characteristics and data
- Tightening torques
- Tools
- Clutch removal and refitting
- Removal
- Checks
- Refitting
- Thrust bearing removaland refitting
- Hydraulic clutch drive
- Hydraulic clutch drive removal - refitting
- Removal
- Refitting
- Pedal board removal - refitting
- Removal
- Refitting
- Pedal board
- Clutch with automatic wear recovery - combined with 6 as’300 vd gearbox
- Description
- Operation
- Removal and refitting ofclutch with device recovery combined
- Removal
- Refitting
- Checks
SECTION 4 - TRANSMISSION
Transmission
- Diagnostics
- Transmission removal - refitting
- Removal
- Refitting
- Gear control check and adjustment
- Gear control
- Flexible cable replacement
- Removal
- Refitting
- Gear shift lever support
- Removal
- Refitting
- 5 s 300 transmissions
- General
- Gear selection and engagement control
- Safety devices
- Specifications and data
- Tightening torques
- Tools
- Overhauling the transmission
- Checks
- 6 s 400 o.d. Transmission
- General
- Gear selection and engagement
- Specifications and data
- Tightening torques
- Tool
- Overhauling the transmission
- Checks
- 6 s 400 a o.d. Transmission
- General
- Main components location
- Main system functions
- Hill holder (function only available to vehicles with esp8 braking system)
- System structure
- Gear selection and engagement
- Specifications and data
- Tightening torques
- Tools
- Diagnosis
- Modus - it 2000 - e.a.sy. Connection
- Gearbox removal/refitting
- Gearbox unit overhauling
- Control unit
- Clutch actuator
- Gearbox actuator
- Chassis wiring gearbox
- Gearbox wiring -gearbox
- Calibration
- Power take off
- Specifications and data
- Tightening torques
- Assembly standards
- Power take off electric actuator
SECTION 5 - PROPELLER SHAFTS
Propeller shafts
- Characteristics and data
- Diagnostics
- Tightening torques
- Tools
- Propeller shaft removal and refitting
- Removal
- Refitting
- Checking propeller shafts on vehicle
SECTION 6 - REAR AXLES
Rear axles
- Diagnostics
- Rear axle nda rs
- Description
- Specifications and data
- Tightening torques
- Tools
- Rear axle nda - rs removal - refitting
- Overhauling the rear axleassembly
- Repairing the differential
- Rear axles nda rg
- Description
- Specifications and data
- Tightening torques
- Tools
- Overhauling the rear axle assembly overhauling therear axle assembly
- Rear axles 450511
- Description
- Specifications and data
- Tightening torques
- Tools
- Rear axle removal - refitting
- Overhauling the rear axle assembly
- Differential repair operations
- Rear axle 450517/2
- Description
- Characteristics and data
- Tightening torques
- Tools
- Rear axle removal - refitting
- Overhaul of rear axle
- Differential repair operations
SECTION 7 - AXLES
Axles
- Diagnostics
- Axle 5817
- Description
- Specifications and data
- Tightening torques
- Tools
- Removing and refitting axle 5817
- Repairs
- Overhauling axle 5817
- Stub axle removal-refitting
- Axle 5818
- Description
- Specification and data
- Tightening torques
- Tools
- Overhauling axle 5818
- Stub axle removal and refitting
- Axle 5819
- Description
- Specification and data
- Tightening torques
- Tools
- Repair operations
- Axle 5819 overhaul
- Axle 5823
- Description
- Specification and data
- Tightening torques
- Tools
- Removing and refitting axle 5823
- Axle 5823 overhaul
- Wheel geometry
- Description
- Wheel geometry
- Specifications and data
- Tightening torques
- Tools
- Checking characteristic angles
SECTION 8 - SUSPENSIONS
Suspensions
- Front and rear mechanical suspensions
- Diagnostics
- Front mechanical suspensions
- Rear mechanical suspensions
- Rear air suspensions
- Diagnostic
- General
- Pneumatic suspensions -wabco type (for 29l - 35s vehicles)
- Specifications and data
- Electric system wabco (ecas)
- Pneumatic system wabco (ecas)
- Pneumatic system on vehicle
- Chassis self-levelling, lifting and lowering
- Main system components
- Pneumatic supply unit
- Electronic control unit
- Level sensor
- Air spring
- Load sensing valve
- Rear suspension overhaul
- Leaf spring
- Rear shock absorbers
- Rear stabilizer bar
- Panhard reaction bar
SECTION 9 - WHEEL AND TYRES
Wheel and tyres
- Description
- Tyre pressure
- Tools
- Fault diagnosis
- Static wheel balancing
- Tyre pressure
- How tyre behaviour depends on pressure
SECTION 10 - STEERING GEAR
Steering gear
- Steering gear
- General
- Power steering specifications and data
- Steering gear
- Tightening torques
- Specific tools
- Diagnostics
- Power steering
- Description
- Power steering type trw
- Operation
- Power steering type zf
- Operation
- Checks and operations on the vehicle
- Checking maximum pressure
- Checking hydraulic steering centre (for ”zf”power steering only)
- Bleeding the air from the hydraulic system
- Swivel heads
- Protection casings
- Steering gear control
- Vehicles equipped with an air-ba
- Safety standards to be observed during repair or maintenance operations on vehicles equipped withair-bag system provided by supplier
- Preliminary standards
- Repairs and inspections required after anaccident
- Accidents with or without air-bag module activation
- Accidents with air-bag module activation
- Painting
- Risks for health
- Overexposure effects
- Safety standards to observe when handling air-bag modules
- Air-bag module scrapping
- Safety standards to observe when handling pretensioners
- Pretensioners scrapping
- Operations on system components
- Removing and scrapping activated air-bagmodule and pretensioner from vehicle
- Removing and scrapping non-activated air-bag module from a repairable vehicle
- Air-bag module deployment remote activation
- Activating air-bag modules and electronic pretensioners installed on unrecoverable vehicles
- Upper steering gear shaft removal
- For vehicles equipped with air-bag
- For all vehicles
- Refitting
- Lower steering gear shaft removal
- Refitting
- Hydraulic power steering
- Hydraulic power steering removal
- Refitting
- Hydraulic power steering
- Hydraulic power steering removal
- Refitting
- Steering linkage replacement
- Removal
- Refitting
- Rubber bushing replacement procedure
- Power steering pump
- Power steering pump overhaul procedure
SECTION 11 - HYDRO-PNEUMATIC SYSTEM - BRAKES
Hydro-pneumatic system - brakes
- Graphic symbols for air/hydraulic system circuit diagrams (miscellaneous and generators)
- Graphic symbols for air/hydraulic system circuit diagrams (valves)
- Graphic symbols for air/hydraulic system circuit diagrams (tanks and accumulators)
- Graphic symbols for air/hydraulic system circuit diagrams (converters, cylinders and calipers)
- Graphic symbols for air/hydraulic system circuit diagrams (calipers and cylinders)
- Graphic symbols for air/hydraulic system circuit diagrams (semi-couplings and coupling heads)
- Graphic symbols for air/hydraulic system circuit diagrams (indicators and switches)
- Pipes and couplings
- General
- Re-flanging rigid pipes
- Bending rigid pipes
- Cutting rigid pipes
- Replacing flexible hoses with threaded couplings
- Replacing flexible hoses with quick release couplings
- Braking system
- Outline diagram for vehicles 29l - 35s without abs
- Outline diagram for vehicles 29l - 35s with abs 8
- Outline diagram for vehicles 29l - 35s with esp 8
- Outline diagram for vehicles 35c - without abs
- Outline diagram for vehicles 35c with abs 8
- Outline diagram for vehicles 35c with esp 8
- Outline diagram for vehicles 40c - 45c - 50c - 60c - 65c with abs 8
- Outline diagram for vehicles 40c-45-50c-60c-65 with esp 8
- Braking system main components layout
- Location of the main brake system components on vehicles with abs
- Location of the main brake system components on vehicles with esp
- Description
- Service brake
- Emergency brake
- Parking brake
- Brakes
- Front and rear disc brakes
- Fault diagnosis
- Diagnosis instruments
- Tightening torques
- Tools
- Specifications and data - hydraulic system
- Specifications and data - brakes
- Checks
- Functional check of vacuum brake system
- Braking system main components
- Vacuum pump
- Vacuum servo brake
- Bleeding air from the hydraulic circuit (vehicles not equipped with abs)
- Bleeding air from the hydraulic circuit with deaerator device (vehiclesnot equipped with abs)
- Air bleeding from the abs/esp system hydraulic circuit
- Abs 8/esp 8 system bleeding procedure sequence
- Mechanically controlled load sensingvalve (vehicles 35c)
- Regulation of load proportioning valve on vehicle
- Dual mechanically controlled load sensing valve (vehicles 29l - 35s)
- Adjusting the load sensing valve
- Stability control and anti-skid devices
- Abs system functions
- Antilock braking system (abs)
- Electronic braking distribution device (ebd)
- Electronic stability program (esp) - option
- Functions included in the esp system only
- Acceleration drive control device (asr)
- Engine braking torque control (msr)
- Hill holder control (hhc)
- Hydraulic brake assistant (hba)
- Electro-hydraulic modulator/control unit for 29l - 35s vehicles )
- Electro-hydraulic modulator/control unit for 29l - 35s vehicles )
- Rev sensor
- Phonic wheels
- Esp system sensors
- Yaw sensor with built-in side acceleration sensor
- Longitudinal acceleration sensor
- Steering angle sensor
- Brake repair operations
- Front brakes
- Replacing brake linings
- Checks
- Removal/re-fitting of brake calipers
- Rear brakes
- Removal/refitting of brake calipers
- Checks
- Removal/refitting brake calipers
- Overhaul of brake calipers
- 2x44 - 2x48 - 2x60 brembo brake calipers
- 1x52 - 1x60 brembo brake calipers
- Overhaul of brake discs
- Machining and grinding ofdisc brakes
- Overhauling parking brake
- Wheel nut tightening sequence
- Assembly
- Adjusting parking brake
- Steering angle sensor
- Replacing
- Replacing the esp components
- Calibration
- Longitudinal acceleration sensor
- Removal
- Refitting
- Calibration
- Yaw sensor
- Removal
- Refitting
- Calibration
- Electrohydraulic modulator/control unit
- Removal
- Refitting
- Programming
- Calibration
- Bench overhauling
- Disassembly
- Assembly
SECTION 12 - BODYWORK - CHASSIS FRAME - CAB AIR-CONDITIONING
Bodywork - chassis frame - cab air-conditioning
- Safety standards to observe when working on vehicles equipped with the air-bag system
- Cab air-conditioning
- General
- Ventilation
- Description
- Air-conditioning system main components and functional diagram
- Air-conditioning and heating
- Description
- Air-conditioning
- Heating
- Main components
- Compressor
- Condenser
- Drier filter
- Expansion valve
- Evaporator
- Control and safety devices
- Description
- Three-level pressure switch
- Outside air temperature sensor
- Air-conditioning unit (“m. Marelli” or “denso” type)
- General
- Electronic control unit
- ”m. Marelli” type heater/air-conditioner unit
- Components
- Heater unit
- Components
- Procedure for emptying andrefilling the air-conditioning systems with r134a refrigerant
- R134a refrigerant recovery and refillingstation (99305146)
- Control fascia
- Safety standards
- Operation flow chart
- Recovering refrigerant from the vehicle system
- Creating a vacuum in the system
- Restoring oil in the system
- Filling the system with refrigerant
- Checking the pressures in the system
- Operations prior to disconnecting the station from the system
- Leak finder for air-conditioning systems with hfc r134a (9905147)
SECTION 13 - SCHEDULED MAINTENANCE
Scheduled maintenance
- Maintenance
- Table of maintenance services
- F1a engine vehicles
- Inspection and/or maintenance interventions (f1a engine vehicles)
- Extra plan operations
- F1c engine vehicles
- Inspection and/or maintenance interventions
- Extra plan operations
- Diagram of check and/or maintenance points
- Maintenance operations
SECTION 14 - ELECTRIC/ELECTRONIC SYSTEM
Electric/electronic system
- Abbreviations and graphic symbols
- General warnings
- Technical codes
- Power network
- Positive network (cba)
- Instrument panel interconnection central units (cpl) “75002”
- Fuses / remote control switches identification
- Internal electrical scheme
- Junction connectors
- Junction connector “l”
- Junction connector “m”
- Junction connector “r”
- Junction connector “h”
- Engine opening central unit (cvm) “75001”
- Fuses / remote control switches identification
- Internal electrical scheme
- Junction connectors
- Junction connectors “a”
- Junction connectors “c”
- Junction connectors “b”
- Junction connectors “d”
- Junction connectors “e”
- Junction connectors “f”
- Negative network
- Earth points
- Battery (20000)
- Bosch kcbi 14v 110a alternator
- Ev 12v - 2.3 kw starter motor
- Junction welds
- Wiring harness section
- Description
- Junction connectors
- Bonnet - instrument panel junction (600/601h)
- Bonnet - instrument panel junction (600/601b)
- Bonnet - instrument panel junction (600/601d)
- Bonnet - instrument panel junction (600/601g)
- Bonnet - instrument panel junction (600/601a)
- Bonnet - instrument panel junction (600/601c)
- Instrument cluster (58919)
- Junction connector
- Display screen
- Steering column switch unit (54030)
- Central instrument panel
- Instrument panel switch assembly (53807)
- Optional box
- Fuses / remote control switches identification
- Opt central unit pin-out
- “can lines” system description
- “c” can line
- “b” can line
- Body computer - (86116)
- Description
- Black cab junction connector “ln”
- Blue instrument panel junction connector “pf”
- Blue bonnet junction connector “av”
- Fitter connector (61071)
- Fitter connector (72068)
- Electronic injection edc16
- Particular features of engines euro 4
- System to reduce pollutants at exhaust
- General
- E.g.r. (exhaust gas recirculation) system
- Operation
- Main system components
- E.g.r. Valve
- Modulator solenoid valve
- Air flow rate meter (flow meter)
- D.p.f. (diesel particulate filter) catalyst
- Description
- Particulate filter (components location)
- Throttle valve assembly
- Replacing the components
- Replacing particulate filter
- Replacing flow meter
- Replacing rail pressure sensor in hydraulic accumulator
- Replacing delta-p sensor
- Replacing engine oil
- Replacing an injector
- Electronic injection control
- Edc system components
- Bosch edc16 control unit
- Control unit connection to the injection cable on engine side (housing a)
- Control unit connection to cab-bonnet cable (housing k)
- Accelerator pedal sensor
- Brake pedal switches (53501)
- Clutch pedal switch (42374)
- Preheat plug electronic centre (f1a/f1c engine)
- Preheat plugs
- R.p.m. / timing sensors (f1c)
- Timing sensor (stroke) (f1c)
- Rpm sensor
- Timing sensor
- Pressure regulator
- Rail (pressure accumulator) f1c
- Pressure sensor
- Air temperature/pressure sensor
- Atmospheric pressure sensor
- Engine coolant temperature sensor
- Fuel temperature sensor
- Injectors
- Electromagnetic junction fan
- Camshaft sensor (f1a) 48042
- Flywheel and rpm sensor
- Characteristics of flywheel rpm and timing system sensors
- Pressure regulator
- Rail (pressure accumulator) f1a
- Pressure sensor
- Injectors
- Air temperature / pressure meter
- Electromagnetic junction fan
- Fuel filter
- Fuel pump / fuel level
- Abs 8/esp 8
- The abs 8 system integrates the following functions
- The esp 8 system, in addition to the ebs 8 system, incorporates the following functions
- Four crossed channel system (x)
- Electro-hydraulic modulator/control unit
- Four parallel channel system (ii)
- Electro-hydraulic modulator/control unit
- Abs 8 control unit pin out (x - crossed channels, ii - parallel channels)
- Esp 8 control unit pin out (x - crossed channels, ii - parallel channels)
- Pin out of central unit asr 8 (4 channels -x)
- (4 channels -ii)
- Esp (electronic stability program) operation
- Control strategy
- Sudden obstacle
- Sudden steering
- Vehicle running on a slippery road
- Asr deactivation strategies
- Recovery strategy in case of component failure
- Warning light legend
- Installing the esp components
- Esp system components and calibration
- Yaw sensor with built-in side acceleration sensor
- Longitudinal acceleration sensor
- Longitudinal acceleration sensor calibration
- Steering angle sensor
- Steering angle sensor calibration
- Esp control unit programming
- Air bag
- General
- System operation
- Intervention logics
- Preliminary rules
- Operations after an accident
- Painting work
- Health hazards
- Effects of over-exposure
- Rules of safety in handling air bag modules
- Air bag module scrapping
- Rules of safety in handling pretensioners
- Scrapping pretensioners
- Operations on system components
- Removing and scrapping an activated air bagmodule and pretensioner from a vehicle
- Removing or scrapping an air bagmodule thathas not been deployed from a reparable vehicle
- Deployment of an air bag
- Deployment of air bag modules and electronic pretensioners still on board of irreparable vehicles
- De-activating passenger air-bag
- Electronic control unit
- Central unit pin out
- Spiral contact
- Pretensioners
- Operation principle
- Curtain air bag
- Component replacement interventions
- Electronic central unit
- Drive side air bag module
- Passenger side air bag module
- Spiral contact
- Immobilizer
- Operation description
- Keys
- Body computer
- Antenna
- Warning lamp
- Immobilizer new procedures
- 6as 400 a o.d. Vd automatic transmission
- Description of operation
- Electronic management
- Composition of the system
- System control unit
- Connector control unit pin-out - gearbox side (a)
- Connector control unit pin-out - vehicle side (b)
- Gearbox actuator
- Clutch actuator
- Accelerator pedal
- Gear selector
- Remote control switches / fuses assembly
- Pto
- Pto engaging procedure
- Pto disengaging procedure
- Display screen
- Diagnosis (connector eobd)
- Circuit cards
- Card 1: power network
- Card 2: cab interior components
- Card 3: window winders - electric mirrors
- Card 4: cab interior components
- Card 5: various loads
- Card 6a: telma decelerator
- Card 6b: differential locking - heated rear window and windscreen
- Card 7a: air spring suspension
- Card 7b: additional heater - power take-off
- Card 8: cruise control - climate control system
- Card 9a: automatic gearbox
- Card 9b: esp 8
- Card 10: external illumination
- Card 11a: asr
- Card 11b: camera
- Card 12: external illumination
- Card 13a: air bag
- Card 13b: abs8
- Card 14a: edc 16
- Card 14b: edc 16
- Card 15b: cab interior components
- Card 16: “can” lines